In 2020, Mingjie Group MJ-10 tyre pyrolysis plant for sale to Egypt has completed the transportation and installation. Egyptian customers mainly use pyrolysis equipment to treat waste tires. The MJ-10 pyrolysis plant operates in batch mode and has a processing capacity of 10T/D.
The development of the Egyptian tyre pyrolysis recycling project demonstrates an innovative path for developing countries to address solid waste challenges. Through government guidance, enterprise participation and technological innovation, Egypt is gradually establishing a sustainable waste tire treatment system.
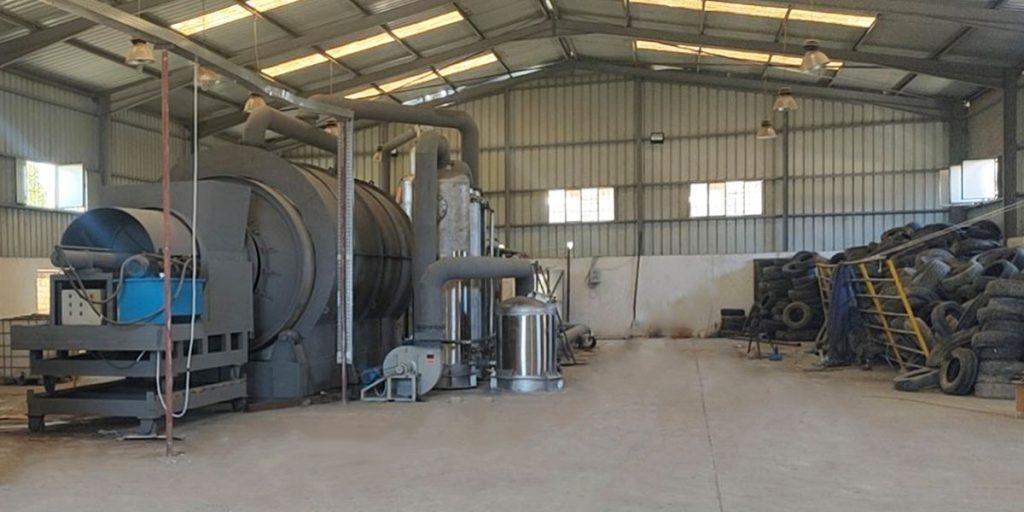
Tire Pyrolysis Project in Egypt
Egypt, as the third most populous country in Africa and an important automobile market, produces a large number of used tires every year. It is estimated that Egypt produces more than 200,000 tons of used tires every year. And with the growth of car ownership, this number continues to rise.
For a long time, the main ways of disposing of used tires in Egypt include:
- Open stacking (fire hazard and mosquito breeding)
- Informal recycling (security risks)
- Partial export processing (expensive)
- Landfill treatment (occupying valuable land resources)
These traditional treatments not only waste resources, but also pose a serious threat to the environment and public health.
In recent years, the Egyptian government has begun to attach importance to the development of circular economy, and the utilization of waste tires as a priority. The “Solid Waste Management Law” issued by the Egyptian Ministry of Environment in 2020 clearly requires the environmental treatment of waste tires, and prohibits open burning and random stacking. In this context, tire pyrolysis technology has become a key solution to be promoted in Egypt due to its efficient resource recovery and environmentally friendly characteristics.
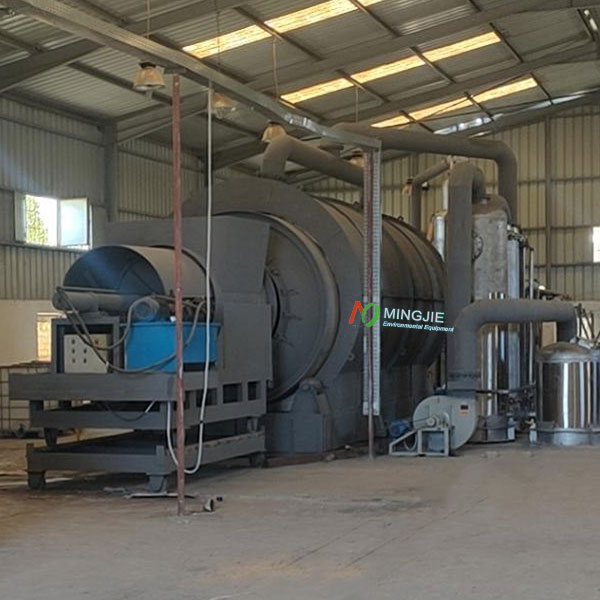
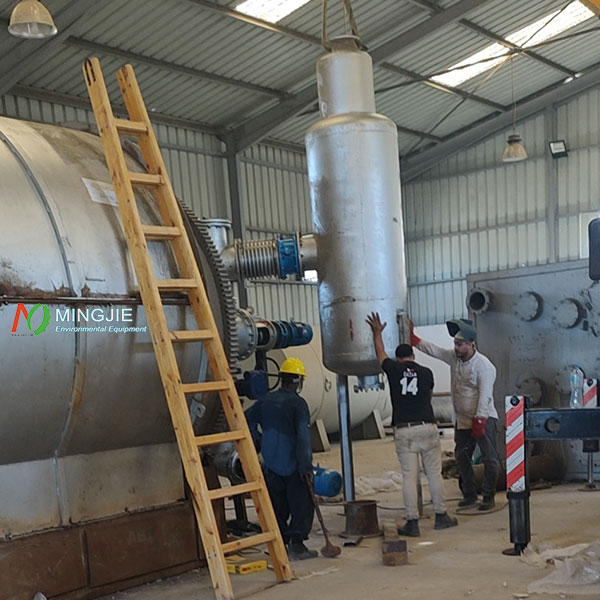
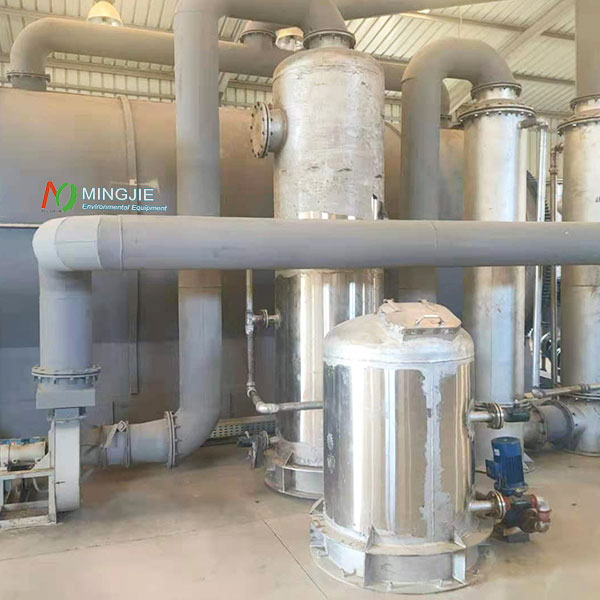
Tyre Pyrolysis Plant for Sale
Tire pyrolysis technology is an emerging resource processing method. It converts waste tires into high-value-added products through high-temperature anaerobic decomposition, providing an innovative solution for the development of the circular economy.
Mingjie Group has developed technically and commercially proven tyre pyrolysis plant for sale. These pyrolysis plants can sustainably turn waste into renewable energy, while improving CO2 emissions and achieving a closed loop.
Mingjie tyre pyrolysis plant for sale is divided into continuous pyrolysis equipment, semi-continuous pyrolysis plant, batch pyrolysis equipment and small pyrolysis plant. Continuous plastic pyrolysis equipment can realize automatic and continuous feeding and slag discharge. Batch plastic pyrolysis plant requires manual operation to realize feeding and slag discharge.
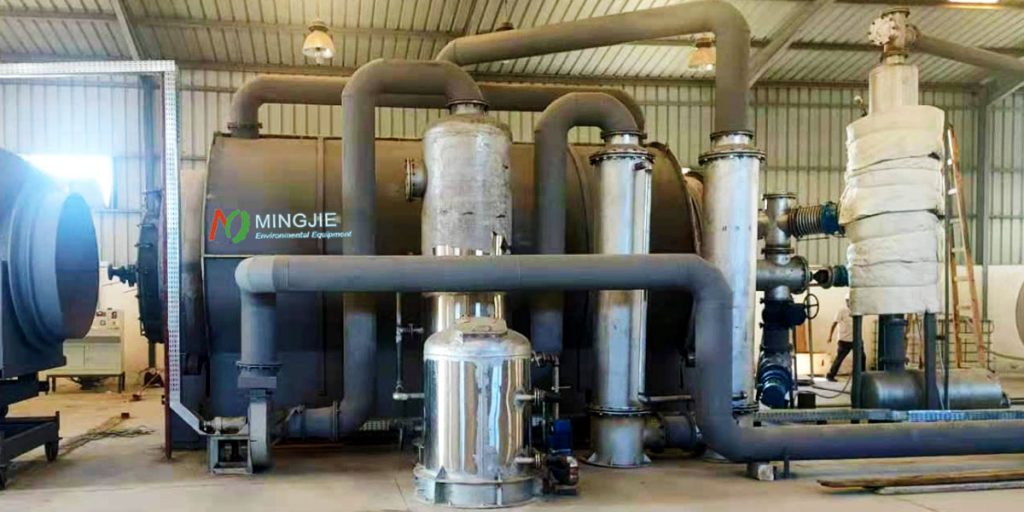
MJ-10 Tire Pyrolysis Plant
The MJ-10 is a batch pyrolysis plant that can process 10 tons of waste per day, such as waste tires, plastics, municipal solid waste, medical waste and oil sludge.
Batch pyrolysis refers to the operation mode that materials enter the reactor in batches, and after completing a complete pyrolysis cycle (feeding-pyrolysis-cooling-discharging), the next batch of processing is carried out. Compared with the continuous pyrolysis system, the batch pyrolysis equipment has significant differences in structural design, operation mode and production process, and is particularly suitable for the pyrolysis needs of small and medium-sized materials.
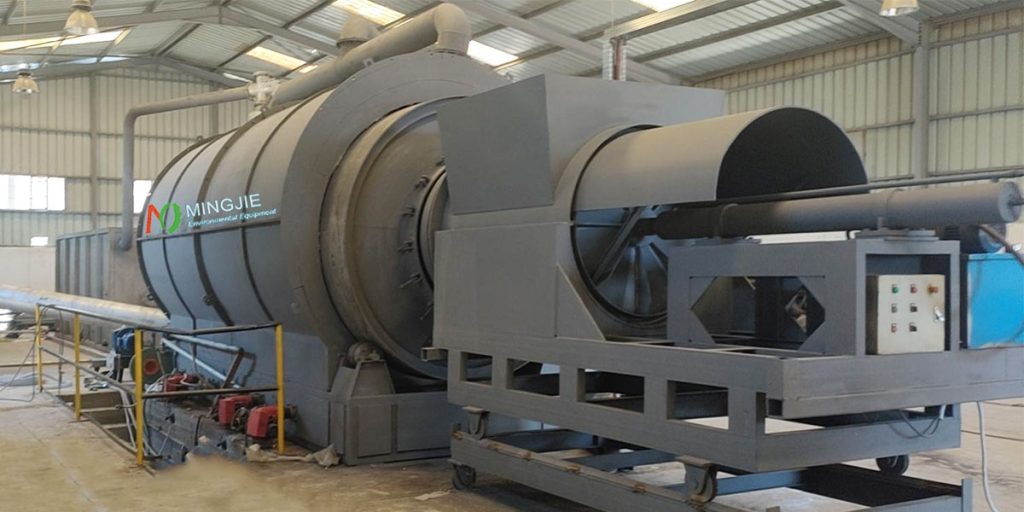
Advantages of Batch Pyrolysis Equipment
1. Low investment cost
- Simple equipment structure: complex conveying systems such as continuous feeding and discharging are omitted.
- Small footprint: A single device usually occupies no more than 100 square meters.
- Low initial investment: Under the same processing capacity, the investment amount is about 30-50% of the continuous type.
- Modular expansion: The production capacity can be flexibly expanded by increasing the number of units.
2. Flexible operation
- Strong adaptability of raw materials: can process mixed waste tires of different sizes and compositions.
- Adjustable process parameters: temperature, time and other parameters can be set independently for each batch.
- Convenient start and stop: suitable for discontinuous production or seasonal raw material supply.
- Easy maintenance: shutdown of a single device for maintenance does not affect the operation of other units.
3. High quality of final product
- Full pyrolysis: static treatment ensures uniform heating of materials.
- High product purity: controllable oil and gas residence time, less secondary cracking.
- Good carbon black quality: no particle refinement problem caused by mechanical wear.
- High oil stability: batch-to-batch quality difference is less than 5% of continuous type.
4. High energy efficiency
- Low thermal inertia: only the current batch of materials needs to be heated, and the ineffective energy consumption is low.
- High waste heat utilization rate (up to more than 75%).
- Sufficient gas self-use: the generated pyrolysis gas can be fully used for heating this batch.
- No continuous insulation loss: the cooling stage completely stops energy consumption.
5. Environmental protection
- Centralized exhaust gas treatment: The amount of exhaust gas generated in a single batch is small and can be centrally purified.
- No continuous emissions: Exhaust gas is only generated during the pyrolysis stage.
- Low risk of leakage: Static seals are more reliable than dynamic seals.
- Fast emergency response: Single batch operations can be interrupted immediately when problems are found.
6. Safe and reliable
- Precise pressure control: Batch operation allows for more precise pressure management.
- Low impact of failure: Problems are limited to a single batch.
- High visibility of operation: Full process monitoring is possible for each batch.
- Complete wire separation: Static discharge ensures complete removal of metal impurities.