Tyre pyrolysis plant can convert waste tires into pyrolysis oil, steel wire, carbon black and syngas. The pyrolysis process does not use oxygen, which makes exhaust emission control simpler and more economical.
Waste Tire/Tyre Pyrolysis Project
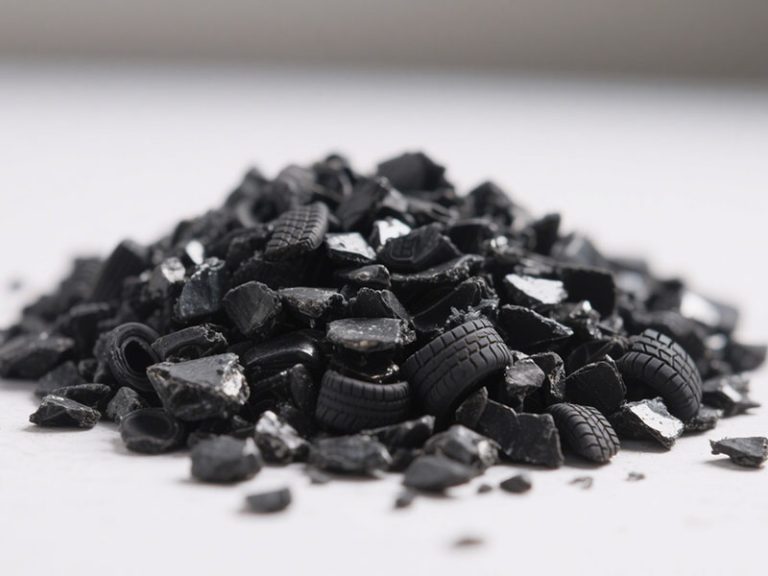
Waste tires are a great potential source of fuel. Pyrolysis plants are able to convert waste into energy. Tyre pyrolysis plant can decompose the rubber component in waste tires into pyrolysis oil, carbon black and syngas.
Among them, pyrolysis oil can be used as fuel oil. Carbon black is widely used in the tire, rubber and plastic industries. And steel wire can be used in the construction and manufacturing industries. Due to the strong market demand for these products, the waste tire oil refining project has significant profit potential.
Main Products of Waste Tire Pyrolysis
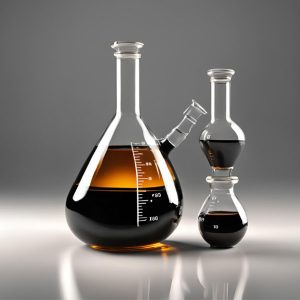
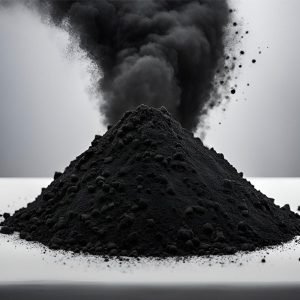
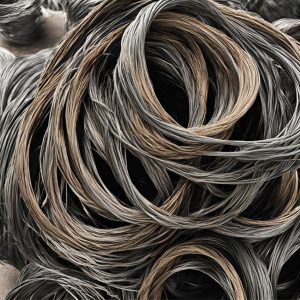
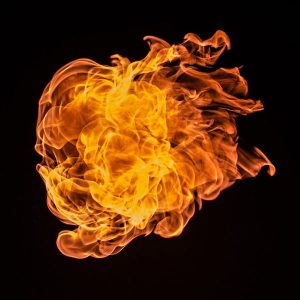
High-quality fuel oil (40%-45%). Heavy pyrolysis oil is the main product obtained from tire pyrolysis refining, and its calorific value is higher than gasoline and diesel. In the energy field, heavy oil can be used for power generation, especially in heavy oil generator sets. This fuel oil has a high calorific value and low sulfur content, and can be used as fuel or further refined into non-standard diesel.
Carbon black (30%-35%). Carbon black is the second largest product of waste tire pyrolysis refining, second only to fuel oil. The carbon black obtained from waste tire pyrolysis is crude carbon black, with a calorific value equivalent to that of coal. Compared with commercial carbon black, it has a larger ash content and lower commercial value, but its value doubles after deep processing. Carbon black is an important industrial material, widely used in tires, rubber products, inks and pigments.
Steel wire (15%). Waste tires contain a large amount of steel wire, which can be recycled through pyrolysis to reduce resource waste.
Syngas (10%). These combustible gases mainly include methane, ethylene and propylene, which can be used for internal heating recycling.
Contact Us To Get Tyre Recycling Pyrolysis Solution
As a professional pyrolysis plant manufacturer, Mingjie Group can provide effective solutions to reduce environmental pollution and recover resources.
Tyre Pyrolysis Plant for Sale
Mingjie tyre pyrolysis plant for sale can be divided into three types according to different processes: Batch Pyrolysis Plant, Semi-continuous Pyrolysis Plant and Fully Automatic Tyre Pyrolysis Plant.
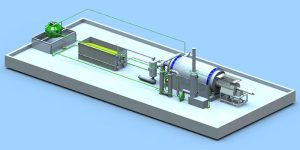
Batch tyre pyrolysis equipment mainly uses whole waste tires as raw materials. The tires do not need to be pre-processed such as cleaning, crushing, wire drawing, etc. They are automatically fed into the cracking furnace directly under the action of the hydraulic loader. The feeding process is highly automated, safe and convenient.
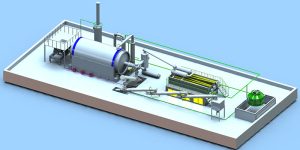
During the whole process, the tire pyrolysis plant has a water cooling system, which is composed of cooling tower and circulation water pool. The circulation water pool keeps providing the cool water for oil condenser, flue condenser and secondary carbon black discharger.
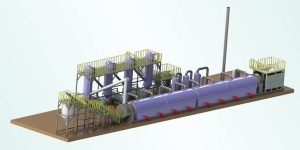
The main difference between continuous and batch tyre pyrolysis machine is that the sludge can be continuously fed, heated and discharged. The feed port and discharge port are sealed by special process settings to achieve the main pyrolysis furnace. The entire continuous process eliminates the cooling link, reduces energy consumption and improves production efficiency.
Tyre Pyrolysis Plant Technical Specifications
Model | Capacity | Reactor Size | Operation |
MJ-2 | 2T/D | D1400*L4000mm | Skid Mounted Batch Type |
MJ-6 | 6T/D | D2200*L6000mm | Batch Type |
MJ-10 | 10T/D | D2600*L6600mm | Batch Type |
MJ-12 | 12T/D | D2800*L7100mm | Batch Type |
MJ-15 | 15T/D | D2800*L8000mm | Batch Type |
MJL-15 | 15-16T/D | D2800*L7100mm | Semi-continuous Type |
MLL-20T | 20-25T/D | L12500*W2200*H2500mm | Fully continuous Type |
MLL-20P | 25-30T/D | D1600*L26000mm | Fully continuous Type |
MLL-30T | 35-40T/D | D1600*L26000mm | Fully continuous Type |
Applicable fuel | Coal/natural gas/LPG/ Diesel/wood/pyrolysis oil | ||
Thickness of Reactor | 16mm/18mm | ||
Cooling method | Water Cooling | ||
Land Required | 300-400m2 | ||
Operating Pressure | Constant pressure |
If you’re interested in purchasing or learning more about tyre pyrolysis equipments, you can contact Mingjie Pyrolysis Plant Manufacturer. Let me know if you need help finding specific models!
Tire Recycling Pyrolysis Plant Application
Waste tires are a common solid waste, which mainly consists of rubber and steel wire. It takes more than a hundred years for waste tires to be decomposed by microorganisms. It is worth noting that the quality of truck tires is very different from other tires, so truck tires are more difficult to handle.
Burning tires will produce smoke, oil and other toxic substances. Considering stricter environmental regulations, energy crisis, fuel consumption, pyrolysis is a more suitable treatment method for waste tires. The tire recycling pyrolysis plant converts waste tires into high-value products, including fuel oil, carbon black and steel wire.
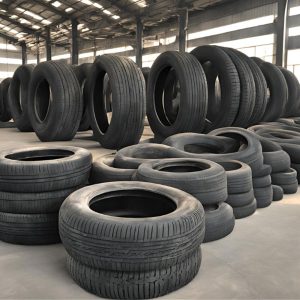

Waste Tire Pyrolysis To Fuel Oil
The tire recycling pyrolysis system is currently the most widely used waste tire oil refining method. Pyrolysis technology decomposes waste tires under high temperature and oxygen-free conditions. It converts organic matter in tires into gas, liquid and solid products.
The tire pyrolysis plant processes waste tires to produce four products: fuel oil, carbon black, steel wire and oil and gas. The fuel oil can be further processed into gasoline, diesel and asphalt if further processed. Our pyrolysis oil distillation plant can further refine the pyrolysis oil.
Tyre Recycling Pyrolysis Process
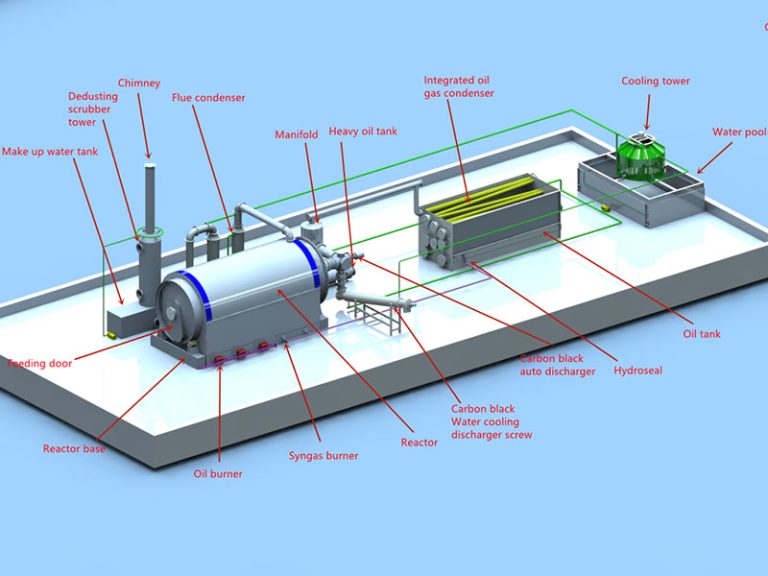
Feeding
First, open the feeding door and put the tire into the reactor manually or by feeding machine. After feeding, close the feeding door.
Pyrolysis
Then, heating the reactor by the burner. The fuel can be LPG, natural gas, or the pyrolysis oil produced by the equipment. When the temperature inside of reactor reach to 120 degrees, there will be mixed oil gas generation that will come to the manifold.
In the manifold, the heavy oil gas will be liquefied and become the heavy oil, which will flow to the heavy oil tank. The light oil gas will keep on rising up and enter the oil gas condenser.
In the oil gas condenser, the light oil gas will be liquefied to pyrolysis oil and flow to the oil storage tank. Un-condensable syngas will come out from the oil storage tank and enter the hydroseal. In the hydroseal, the un-condensable syngas will be cleaned and desulfurized and then recycled as fuel for heating the reactor. The extra syngas will be burned out in the extra syngas burning room for releasing the reactor’s pressure in case the pressure is too high.
Cooling
After the pyrolysis process finished, the reactor needs to be cooled for 4-6 hours. Until the temperature of the reactor is reduced to about 50 degrees, the discharger can be opened, and the carbon black will enter the first carbon black screw discharger, and fall into the secondary water cooling discharger.
During the transport process, due to the water cooling system, the temperature of the carbon black will be reduced. Then the carbon black will be stored in bags, sealed off from air.
After getting out the carbon black, the steel wire will remain in the reactor, open the furnace door to pull out the steel wire. Then load the tire for next batch.
Flue Gas Purification
During the pyrolysis process, due to the combustion of fuel, there will be high temperature smoke generation. High temperature smoke will be first led to the flue condenser by the draft fan, to cool down the temperature of the flue gas. After that go to the dedusting scrubber for cleaning by water washing, ceramic ring adsorption and water spray, then the emission can be discharged into the air through the chimney.