In 2015, Mingjie Group completed the installation of 2 sets MJL-15 waste tire recycling plant for sale to Australia. Australian customers ordered several pyrolysis equipment, mainly for the treatment of waste tires.
MJL-15 is a semi-continuous pyrolysis plant equipped with an automatic feeding system and slag discharging system. The processing capacity of semi-continuous pyrolysis plant is 15-16T/D of tires, and the feed size is 5-8mm rubber particles. The tires are shredded and the steel wires are removed.
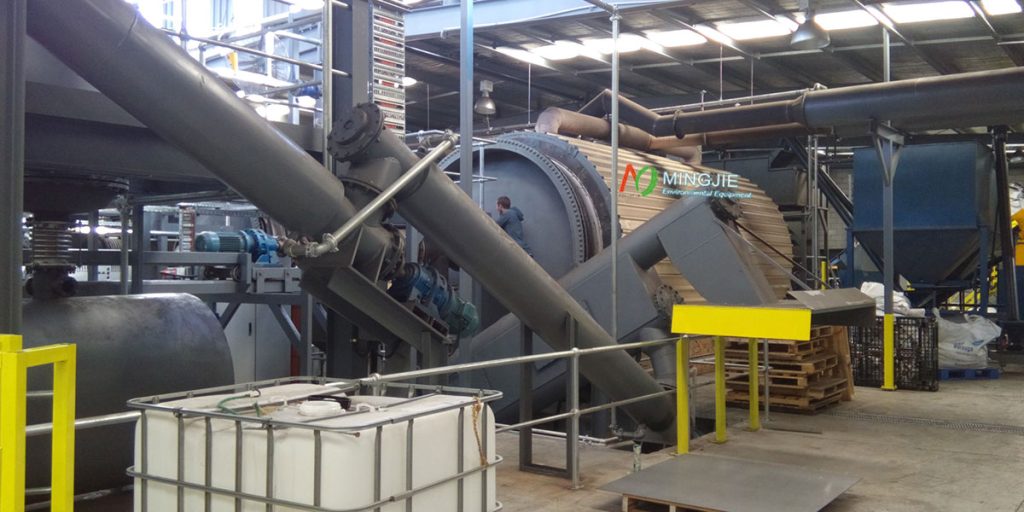
Our tire recycling plant for sale uses a low-temperature oxygen-free pyrolysis process (300-700°C), which is in line with Australia’s high humidity climate conditions. From feeding to discharging, the entire press of the semi-continuous pyrolysis plant is sealed, and the operating environment is clean.
The tire recycling plant for sale adopts an intelligent control system, to achieve real-time monitoring and fault warning of the entire process. The environmental protection treatment module adopts an integrated multi-stage flue gas purification device.
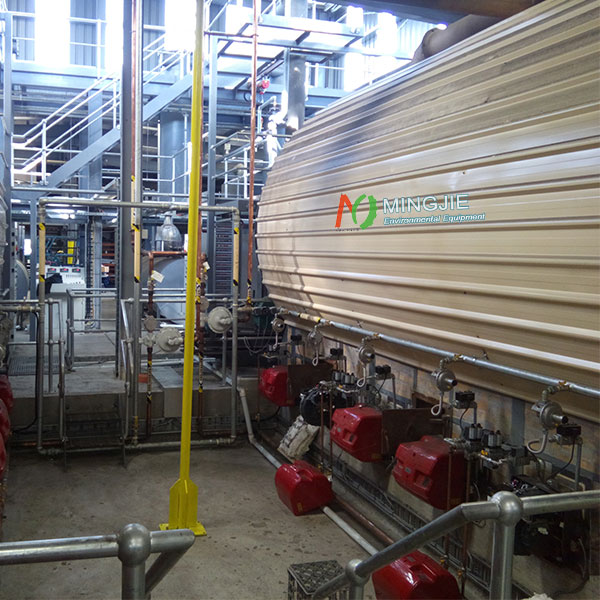
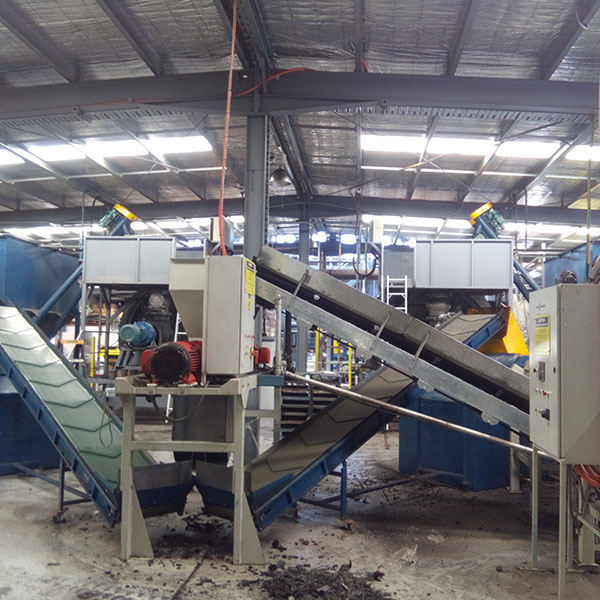
Tire Pyrolysis Project in Australia
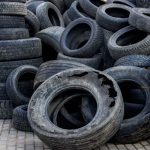
Waste tires are called “black pollution” and their potential threat to the environment cannot be underestimated. In terms of land resources, a large number of waste tires need to occupy a vast space for stacking. In Australia, where land resources are already precious, especially in urban areas, this is undoubtedly a huge waste. Moreover, waste tires are difficult to degrade and will occupy land for a long time, making it difficult for these lands to be effectively used.
Faced with the various difficulties brought by waste tires, Australia has been actively exploring effective solutions. Among the many attempts, the tire pyrolysis project has become a focus of attention.
Australia generates about 45 million (equivalent to 250,000 tons) of waste tires every year, and traditional treatment methods face severe challenges. Pyrolysis plants can transform waste tires from an environmental burden to a strategic resource.
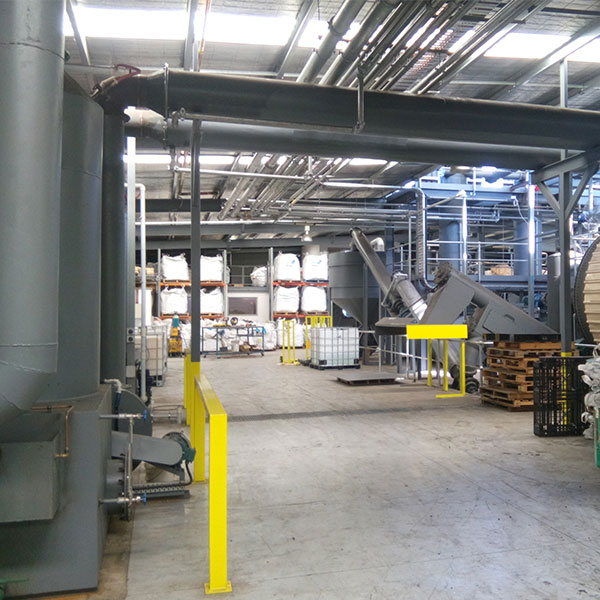
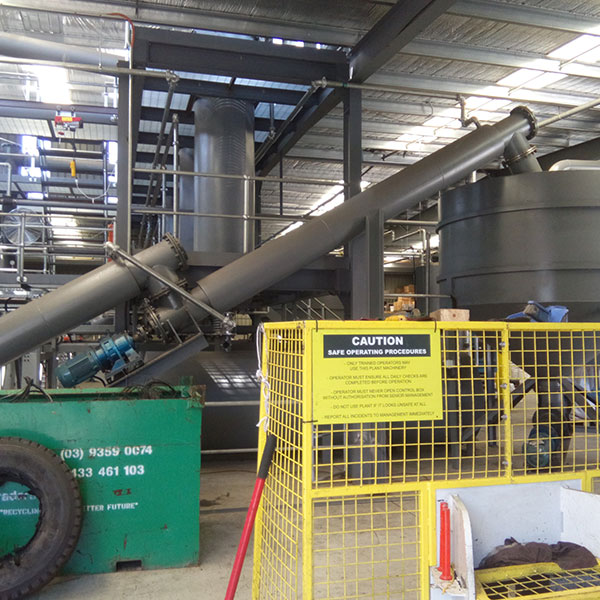
The benefits of the Tire Pyrolysis Project in Australia in the field of environmental protection are very significant. It has greatly reduced the pollution of waste tires to the environment and has also played an important role in reducing carbon emissions.
From the perspective of resource recycling, the tire pyrolysis recycling project perfectly interprets the concept of circular economy. Rubber, carbon black, steel wire and other components in waste tires are separated and reused during the pyrolysis process, realizing the transformation from waste to resources.
Value of Tyre Pyrolysis Products
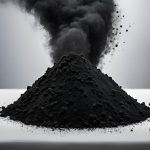
The recycled carbon black produced by the Australian tyre pyrolysis recycling project is of high value, and its performance is very similar to ASTM (American Society for Testing and Materials) carbon black. The recycled carbon black produced by the tire pyrolysis project is comparable to ASTM carbon black in key indicators such as particle size distribution, specific surface area, and structure.
In the production of rubber products, recycled carbon black can replace 10% to 100% of traditional carbon black, which will not only not affect the quality and performance of rubber products, but also reduce production costs.
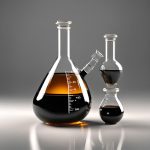
Recycled fuel oil also has significant advantages. It contains about 35-40% bio-based content, which makes it excellent in environmental performance. Compared with traditional fossil fuels, bio-based fuels produce lower greenhouse gas emissions during combustion, which helps to mitigate global climate change.
hIn terms of use, recycled fuel oil has a wide range of uses, of which 85% can be used as marine fuel oil. The pyrolysis oil are further purified into bright non-standard diesel or non-standard gasoline by pyrolysis oil distillation plant. This light fraction oil can be widely used in heavy-load low-speed diesel engines, ships, diesel generators, etc.
Tire Recycling Plant for Sale
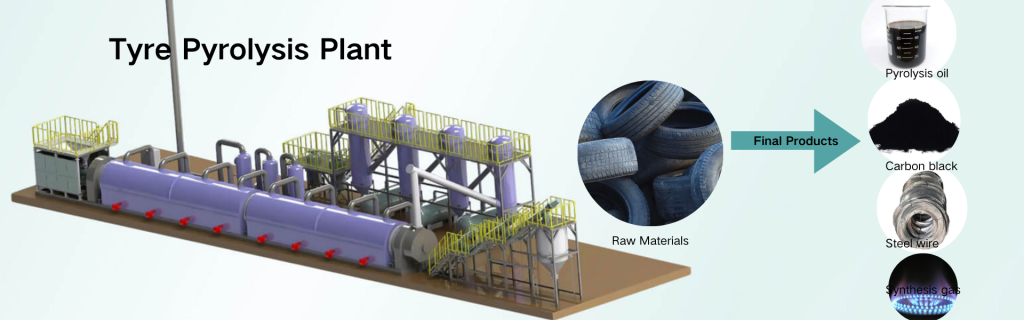
The tire pyrolysis plant can convert waste tires into valuable resources, such as recycled carbon black and fuel oil. Its core principle is based on thermal cracking reaction, which applies high temperature to waste tires in a specific environment without or without oxygen.
Tires are mainly composed of rubber, which is a high molecular polymer. Under the action of high temperature, its complex molecular structure begins to change wonderfully. The polymer chain gradually breaks and decomposes into relatively small molecular fragments. These small molecules are further reorganized and transformed to generate a variety of products, such as fuel oil, carbon black, steel wire and combustible gas.
Tyre Pyrolysis Recycling Process
The tyre pyrolysis recycling process is like a precision-operated industrial production line. Each link is closely connected to complete the gorgeous transformation from waste tires to high-value products.
- The first is the pretreatment stage of waste tires. The surface of the newly collected waste tires is often attached with various impurities, such as soil, stones, metal parts, etc. In order to ensure the smooth progress of the subsequent pyrolysis process, they need to be carefully cleaned and removed.
- Waste tires enter the pyrolysis reactor. In the pyrolysis reactor, the tires are gradually heated in an oxygen-free or low-oxygen environment, and the temperature usually rises to 400-600℃. As the temperature rises, the rubber in the tire begins to undergo pyrolysis reaction, decomposing to produce various gas, liquid and solid products.
- Separation of pyrolysis products. The mixed products produced by pyrolysis first enter the condensation system, the gaseous fuel oil in it is converted into liquid, thereby achieving gas-liquid separation.
- The purification system is used to treat the waste gas generated during the pyrolysis process to ensure that it does not pollute the environment. The automated control system monitors and regulates each link in real time to ensure the stable operation of the pyrolysis process.