Mingjie pyrolysis oil distillation plant can refine tire pyrolysis oil or waste engine oil into diesel or gasoline, making them reach a higher use value. The pyrolysis oil distillation unit is relatively simple to operate, and no secondary pollution will be generated during the distillation refining process.
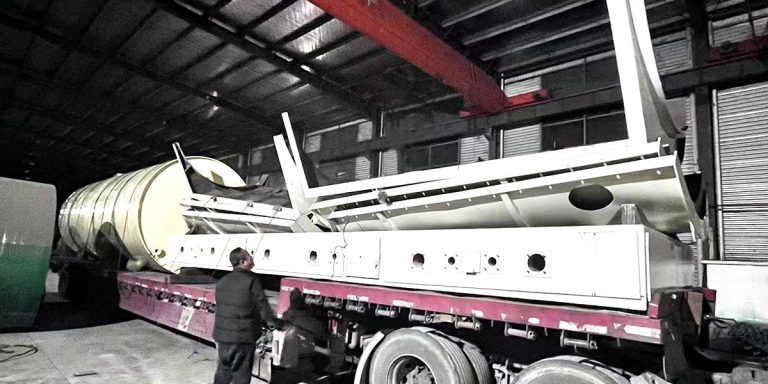
MJZ-20 Used Oil Distillation Plant for Sale to Malaysia
On March 26, 2025, Mingjie Group completed the shipment of MJZ-20 used oil distillation plant for sale to Malaysia. The processing capacity of pyrolysis oil of MJZ-20 waste oil distillation plant is 20T/D. The following are the shipment pictures of the waste oil distillation equipment at Mingjie’s factory. The large
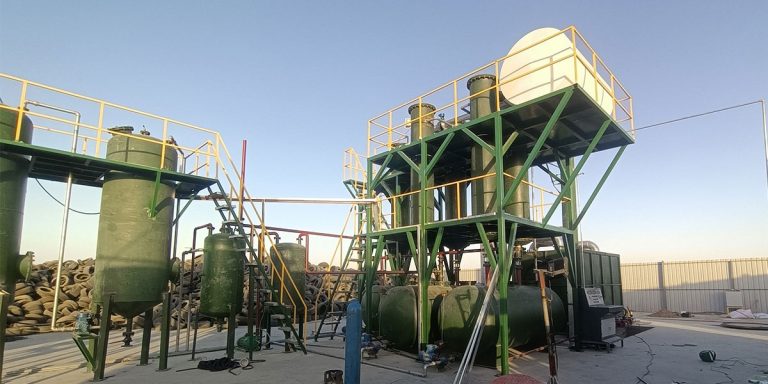
MJZ-6 Waste Oil Distillation Plant for Sale to Iraq
In August 2022, Mingjie Group completed the shipment and installation of the MJZ-6 waste oil distillation plant and pyrolysis equipment for sale to Iraq. The customer needs to process a large amount of waste tires. MJ-10 has a waste tire processing capacity of 10T/D, and MJZ-6 has a pyrolysis oil
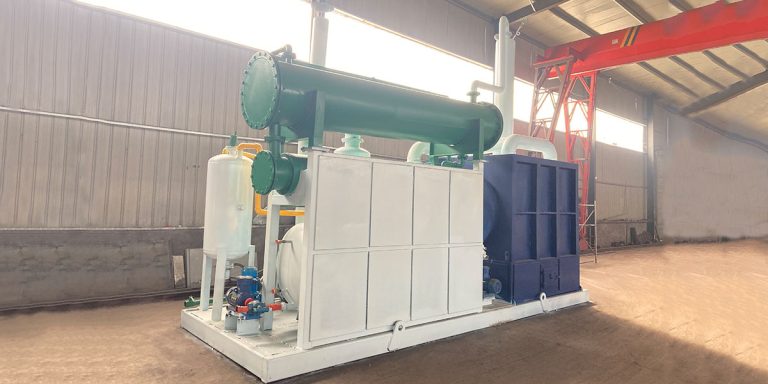
Small Distillation Plant for Sale to Peru
In 2021, Mingjie Group completed the shipment of the MJZ-2 Small Distillation Plant and the MJ-2 Small Pyrolysis Plant for sale to Peru. The MJZ-2 and MJ-2 small equipment both adopt skid-mounted design. The core features of skid-mounted equipment are integrated design, rapid deployment, and flexible relocation. They are suitable
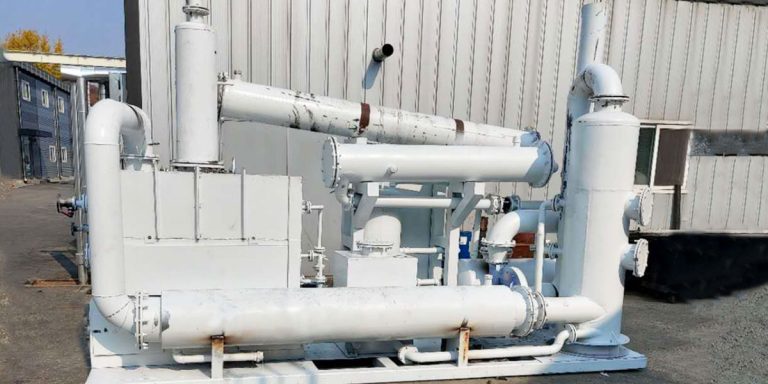
Waste Oil Distillation Machine for Sale to South Korea
In 2022, Mingjie Group completed the transportation and installation of MJZ-2 waste oil distillation machine for sale to South Korea. This is a skid-mounted distillation equipment, it can effectively convert pyrolysis oil and waste oil into diesel or gasoline under high temperature decomposition. The skid-mounted pyrolysis oil distillation equipment is
MJZ-20 Used Oil Distillation Plant for Sale to Malaysia
On March 26, 2025, Mingjie Group completed the shipment of MJZ-20 used oil distillation plant for sale to Malaysia. The…
Mini Distillation Plant for Sale to Paraguay
On May 23, 2025, Mingjie Group completed the shipment of mini distillation plant for sale to Paraguay. The distillation equipment…
MJZ-6 Waste Oil Distillation Plant for Sale to Iraq
In August 2022, Mingjie Group completed the shipment and installation of the MJZ-6 waste oil distillation plant and pyrolysis equipment…
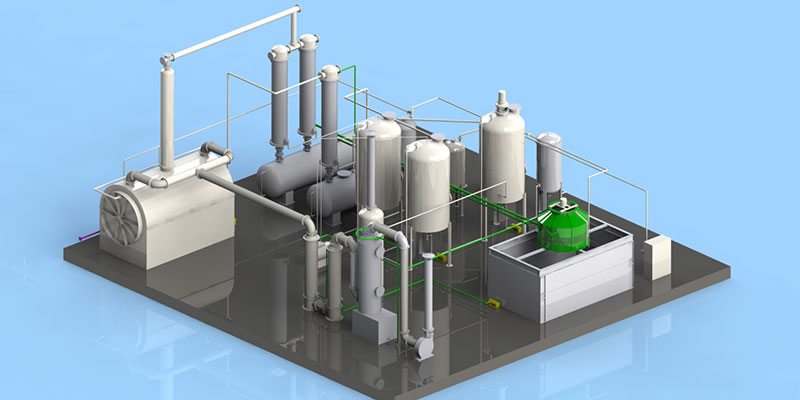
Pyrolysis Oil to Diesel Project
The conversion of plastic pyrolysis oil into fuel oil (such as diesel, gasoline or heavy oil) requires processing through distillation equipment, thereby improving the quality and applicability of the oil. Waste oil distillation equipment plays a vital role in the pyrolysis oil recovery and refining process. The distillation equipment has a high recovery rate, reaching 85-90%. It adopts full-process sealed operation, and the gas that cannot be condensed is discharged after exhaust gas treatment to meet the emission standards. The residual oil that cannot be distilled can be used as heavy diesel for combustion.
Contact Us To Get Pyrolysis Oil to Diesel Solution
As a professional environmental protection equipment manufacturer, Mingjie Group can provide you with the best waste oil distillation equipment and professional services.
Pyrolysis Oil to Diesel by Distillation
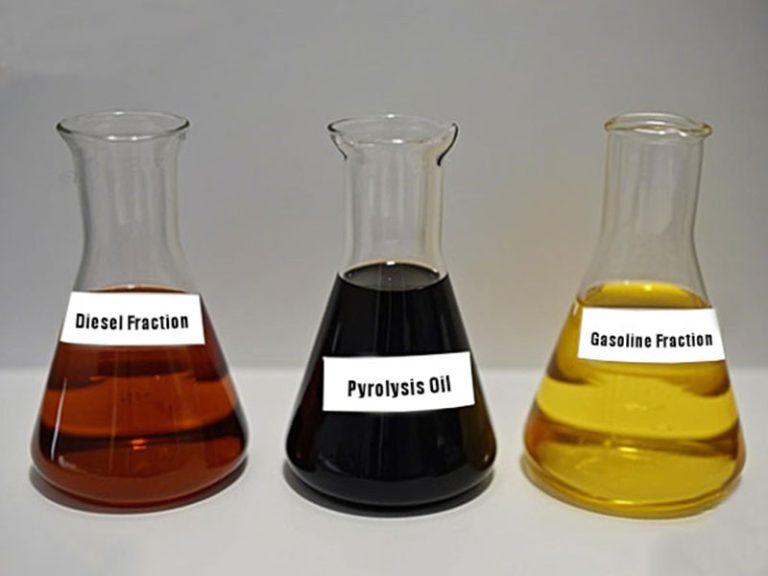
Pyrolysis oil is produced by pyrolysis of solid waste. It is a dark brown viscous liquid with high oxygen content (35%-50%), acidity (pH 2-4), low calorific value (16-19 MJ/kg) and instability.
Mingjie pyrolysis oil distillation plant can convert it into gasoline or diesel under high temperature decomposition. During the pyrolysis oil distillation process, the hydrocarbon molecular chains are destroyed and the molecules are reorganized to form new oil products. Subsequently, the oil is atomized into oil mist, which becomes liquid after condensation, and finally clear diesel is obtained.
Working Principle of Pyrolysis Oil Distillation Plant
Pump the pyrolysis oil into the reactor of the distillation plant. Heat the distillation reactor, and the tyre pyrolysis oil is distilled into oil and gas at high temperature. What remains is the heavy oil residue. The oil and gas are condensed and collected in the storage tank. The collected oil is purified and decolorized to finally obtain clean and transparent diesel.
The process of converting tire pyrolysis oil into diesel in distillation plant is mainly divided into two parts: Pyrolysis Oil Distillation and Oil Gas Refining.
- Pump the pyrolysis oil into the distillation reactor, the hot oil pump will make the oil recycle in the reactor to avoid coking problems.
- Heat the reactor and pyrolysis oil will become the oil gas. The oil and gas pass through the distillation tower to the light fraction condenser, where they are liquefied into oil and finally stored in light oil tanks.
- In the condensing process, there is a part of gas that can not be condensed, the gas will go through the oil tank and vacuum system to the hydroseal.
- In the hydroseal, the syngas will be cleaned and desulfurized, after which, one part will be recycled as fuel for the reactor heating. Another part of extra syngas will be burned out directly in burning room, in case the temperature and pressure is too high in the reactor.
- In the pyrolysis oil distillation process, vacuum system will create a negative pressure environment for the equipment, to make sure safety production.
- During the pyrolysis oil distillation process, high temperature smoke will be generated. Emission will come out from furnace and go through the flue condenser for cooling down the temperature. Then it go through the dedusting scrubber for cleaning by water washing, ceramic rings adsorption and water spray. Finally, the emission can be discharged into the air through chimney without pollution.
- After pyrolysis oil distillation process finished, cool down the reactor for 3-4 hours to reach about 200℃. The remaining heavy oil will be pumped out to oil gas condenser and stored in the heavy oil tank.
- Pump light oil from the storage tank to the pickling tank, add 98% sulfuric acid with a dosage of 2-5%, mix and sediment, which can remove the sulfide and colloid in the oil.
- After pickling washing, pump the oil into the alkaline washing tank for neutralization and remove the oxygenated chemicals, sulfide. Add 40% of the concentration of sodium hydroxide solution with a dosage of about 3%.
- In the pickling and alkaline washing process, the air compressor will provide compressed air to the tanks for mixing function.
- After alkaline washing, pump the oil into the activated clay tank for adsorption of the solid impurities. Slowly add 2-5% activated clay and mix for 2 hours. Meantime, use the steam boiler for heating, so that the oil temperature will be maintained at 70 to 90 degrees.
- After activated clay adsorption process, pump the oil to go through the plate-and-frame filter press to get the final clean and transparent non-standard diesel.
CONTACT US
Please Feel free to give your inquiry in the form below, and we will reply you in 24 hours.