Compared with batch pyrolysis plants, continuous pyrolysis plants have the advantages of high degree of automation, large processing capacity and low energy consumption. According to different operation modes, Mingjie continuous pyrolysis plants are divided into semi-automatic continuous pyrolysis equipment and fully continuous pyrolysis plant.
Semi Continuous Pyrolysis Plant
- Feeding size shall be 5-8mm rubber granule, tyre shall be shredded and steel wire will be removed.
- Processong capacity 15-16T/D tyre, 12T/D plastic.
- Equipped with auto feeder system, feeding can be done at high temperature.
- From feeding to discharging, the whole press is sealed, operation environment is clean.
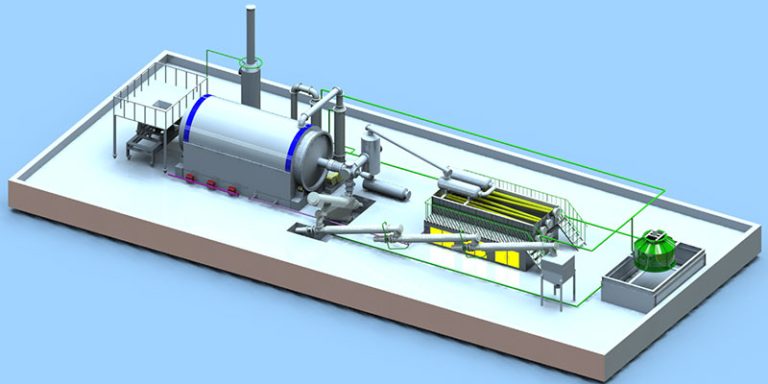
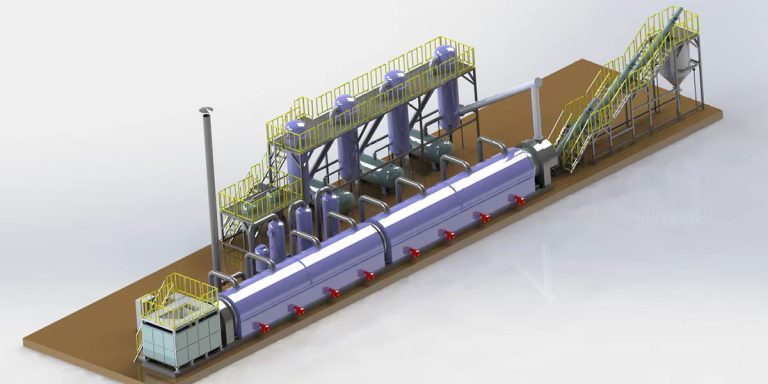
Fully Automatic Pyrolysis Plant
- Feeding size shall be 5-8mm rubber granule, tyre shall be shredded and steel wire will be removed.
- Processong capacity 35-40T/D tyre, 30T/D plastic.
- Fully continuous feeding and discharging in 24hours.
- From feeding to discharging, the whole press is sealed, operation environment is clean.
Model | MJL-15 | MLL-20T | MLL-20P | MLL-30T |
Capacity | 15-16T/D | 20-25T/D | 25-30T/D | 35-40T/D |
Reactor Size | D2800*L7100m | L12500*W2200*H2500m | D1600*L26000m | D1600*L26000m |
Operation | Semi-continuous Type | Fully continuous Type | ||
Applicable fuel | Coal/natural gas/LPG/ Diesel/wood/pyrolysis oil | |||
Reactor Thickness | 16mm/18mm | |||
Cooling method | Water Cooling | |||
Land Required | 300-400m2 | |||
Operating Pressure | Constant pressure |
If you are interested in purchasing or learning more about pyrolysis equipments, you can contact Mingjie Pyrolysis Plant Manufacturer. Let me know if you need help finding specific models!
Continuous Pyrolysis Plant for Sale
Continuous pyrolysis plant realizes large-scale waste recycling projects through continuous feeding and discharging. It is an industrial equipment for efficiently treating organic waste (plastics, tires, or oil sludge). Continuous pyrolysis plant has strict requirements on feed size, and the crushed plastic or rubber must be less than 5-8mm.
The continuous pyrolysis plant can achieve 24-hour continuous operation, with large processing capacity, suitable for large-scale industrial production. It adopts an automated control system to reduce manual operation and improve production efficiency and safety. The closed design reduces exhaust gas emissions, and the gas purification system further reduces environmental pollution.
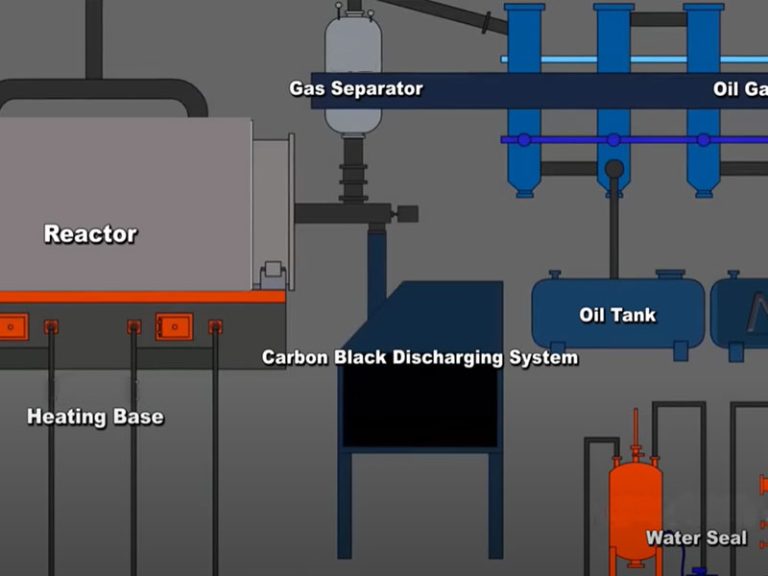
Semi-Continuous Pyrolysis Plant Application
Fully Automatic Pyrolysis Plant Application
Continuous Pyrolysis Plant Advantage
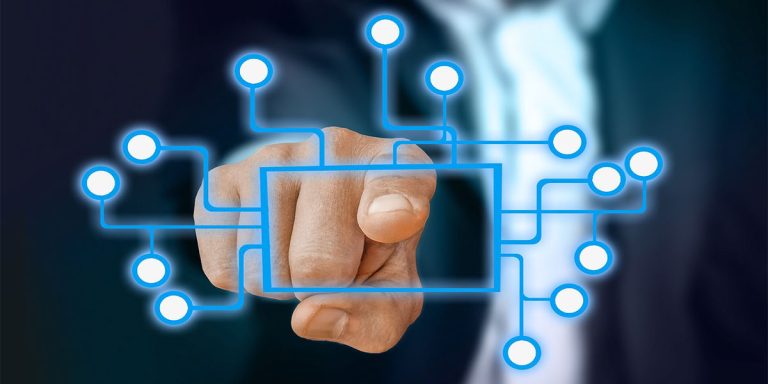
The continuous pyrolysis equipment uses a PLC automated intelligent control system. It can monitor, collect, display, calculate and process each control point in real time and issue corresponding instructions. Intelligent safety operation can achieve automatic deviation correction and automatic alarm.
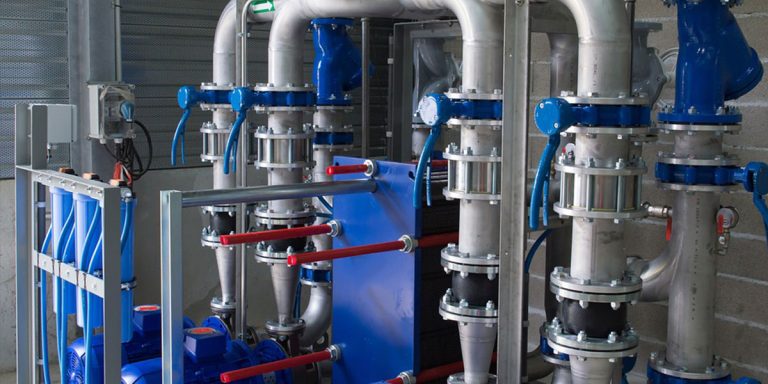
Continuous pyrolysis plants can process solid waste continuously. Feeding and slag discharge can be carried out in cycles. No need to stop and cool repeatedly, saving time. The continuous pyrolysis equipment has a stable processing capacity and is suitable for large-scale production needs. Continuous operation reduces mechanical wear caused by frequent start and stop of equipment and extends service life.
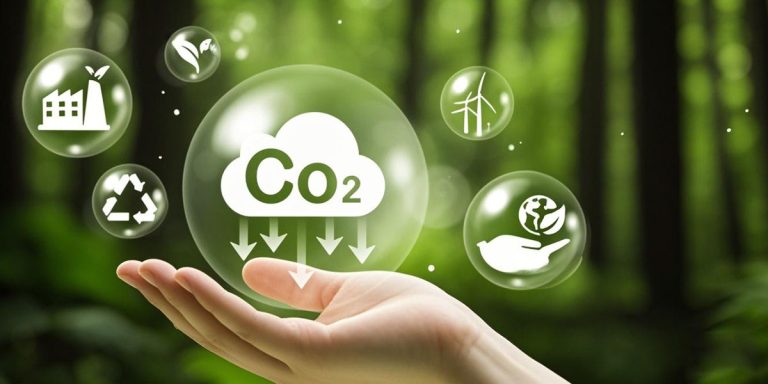
The continuous pyrolysis equipment adopts a closed two-way slag discharge design. It ensures that the solid product is transported in a closed pipeline without dust leakage. The pyrolysis process does not involve incineration, which reduces CO₂ emissions and meets the goal of carbon neutrality. The closed system reduces dust and odor leakage, and controls pollutants through tail gas purification technology. The high-temperature flue gas generated during the pyrolysis process can be used to preheat the raw materials and reduce energy consumption.
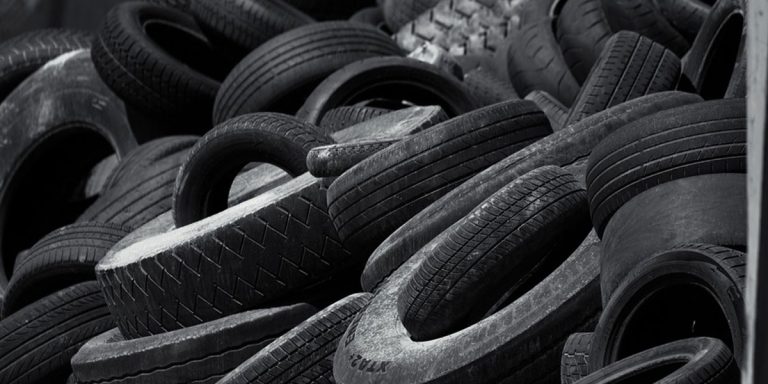
The min processing capacity of a single continuous waste tire pyrolysis plant is 15 T/D, and the max capacity is more than 50 T/D. The complete material conveying system can shorten the residence time and increase the processing capacity per unit time.
How to Achieve Continuous Pyrolysis
1. Preprocessing
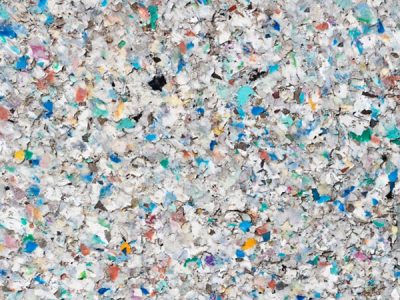
- Classify plastics by type and remove impurities such as PVC, PET plastics and metals, paper, etc.
- Put the large raw materials into the crushing machine to make the size less than 5-8mm.
- If the plastic contains oil or attachments, it needs to be cleaned (such as soaking, spraying) and dried in advance.
- The crushed material enters the drying machine with an auger to evaporate the water.
2. Pyrolysis Process
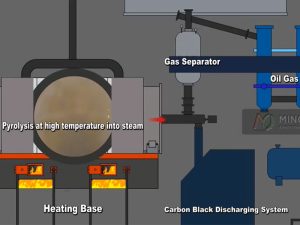
The material is gradually heated in the pyrolysis reactor, and further dehydrated and initially pyrolyzed at about 150-350℃.
The water and light component oil are cooled in the initial distillation section, the liquid enters the storage tank, and the gas is sent to the heating furnace for combustion.
The material continues to enter the high temperature of 500-700℃ to be fully heated.
3. Pyrolysis Products Collection
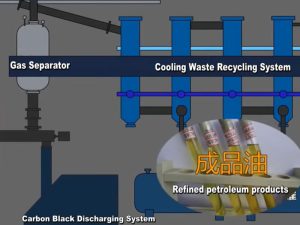
The generated oil, gas and dust enter the separator and are cooled. The liquid fuel oil enters the storage tank, and the synthesis gas is sent to the heating furnace for combustion.
The slag carbonized by high-temperature pyrolysis enters the first-stage slag discharger for discharge, then enters the second-stage cooling slag discharger for cooling, and then enters the third-stage dust removal and slag discharger, and finally discharged to the storage tank.
4. Flue Gas Purification
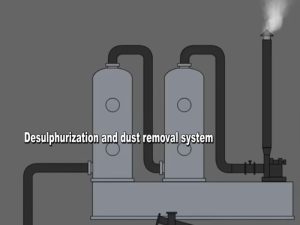
After the non-condensable gas enters the purification processor system for treatment, it is sent to the heating furnace for combustion and heats the reactor.
The flue gas from the heating furnace can reheat the raw materials. Then, it enters the flue gas treatment system for purification and discharge.