Modern biomass carbonization plant can efficiently convert biomass into biochar by pyrolysis technology. It is able to produce clean energy and reduce carbon emissions. Biomass carbonization plant is also called Biomass Pyrolysis Plant, Biochar Production Equipment, Biomass Charcoal Making Machine.
Biomass Carbonization Plant for Sale
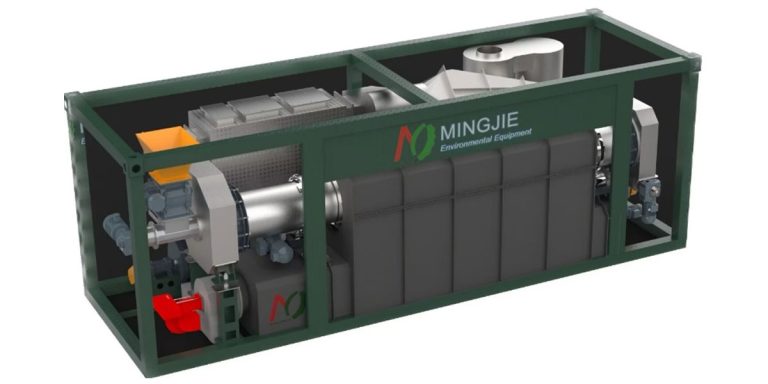
According to the different biochar making machine structures, Mingjie biomass carbonization plant can be divided into skid-mounted small biomass pyrolysis plant and modular continuous biomass to biochar making machine.
The small biomass pyrolysis machine adopts an integrated skid-mounted structure, and the capacity of processing waste biomass is 50-100kg/h. The skid-mounted carbonization equipment tightly integrates the pyrolysis reactor, cooling system, intelligent control module and purification system.
The double-barrel reactor can improve the continuity and reliability of the use of pyrolysis equipment, and realize the integration of material drying and carbonization. It can ensure that the content of the produced biomass carbon meets the ideal requirements.
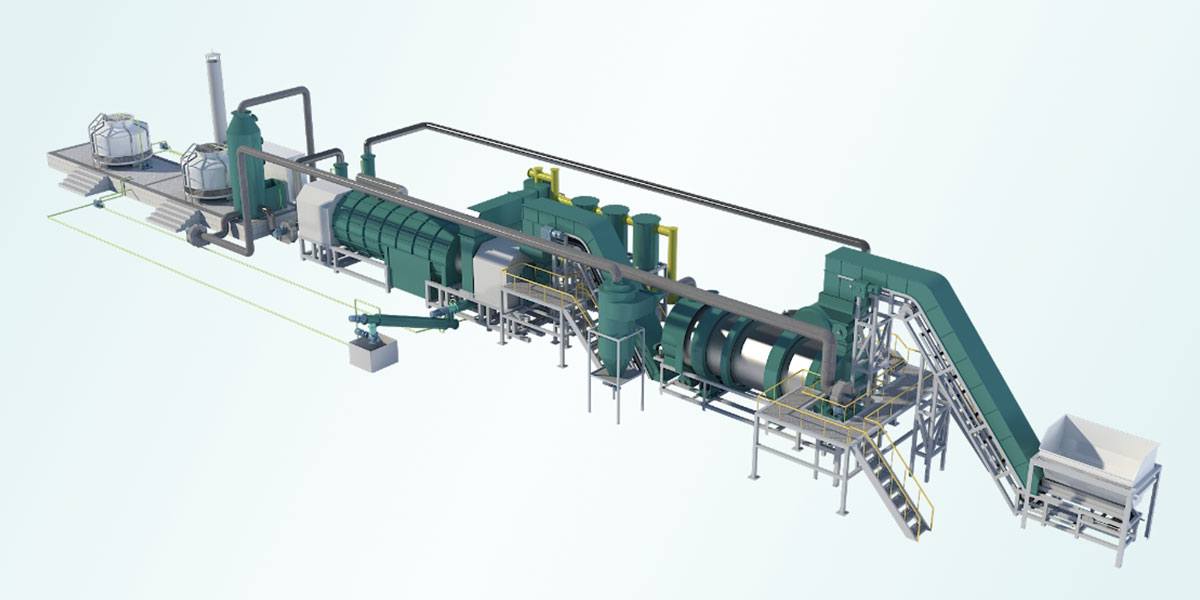
The biomass carbonization plant realizes the continuous feeding of biomass and the continuous discharging of biochar, which can meet the needs of large-scale industrial production. The large-scale biochar making machine is equipped with an automatic feeding conveyor belt and a spiral discharging device. The biomass raw materials continuously enter the pyrolysis reactor through the conveyor belt. After the pyrolysis process is completed in the reactor, the biochar is continuously output by the spiral discharging device.
If you’re interested in purchasing or learning more about biomass pyrolysis machines, you can contact Mingjie Biomass Carbonization Plant Manufacturer. Let me know if you need help finding specific models!
Biochar Making Machine Technical Specifications
Model | MJT-100 | MJT-500 | MJT-1000 | MJT-2000 | MJT-3000 | MJT-5000 |
Input Capacity | 50-100kg/h | 300-500kg/h | 800-1000kg/h | 1500-2000kg/h | 2500-3000kg/h | 4500-5000kg/h |
Structure | Skid Mounted | Modularized | Modularized | Modularized | Modularized | Modularized |
Reactor Type | Single Layer | Dual cylinder | ||||
Working Method | Fully Continuous | |||||
Reactor Material | 304 Stainless steel | |||||
Feedstock Size | <20mm | |||||
Feeding Moisture | <15% | |||||
Initial Heating Oil Consumption | 20L | 30-40L | 35-50L | 50-70L | 80-90L | 120-140L |
Land Area | L12m*W2.5m | L29m*W12m | L34m*W13m | L36m*W15m | L42m*W15m | L50m*W18m |
Advantages of Mingjie Biomass Carbonization Plant
- The pyrolysis reactor is a double-layer design, and the heat utilization rate is more than doubled compared with the single-layer external heating structure.
- The material is stainless steel, which can withstand a wider range of temperature changes and extend the service life of the equipment.
- The fully enclosed heating chamber meets higher environmental protection standards.
- Hot air heating, the flame will not contact the main machine, making the heating more uniform and helping to extend the service life of the machine.
- Higher standard emission cleaning system, including wet scrubber, activated carbon treatment, ultraviolet light, etc.
- The special sealing system makes the equipment safer and the performance more stable.
If you’re interested in purchasing or learning more about biochar production equipments, you can contact Mingjie Biomass Carbonization Plant Manufacturer. Let me know if you need help finding specific models!
Biomass Pyrolysis Carbonization Project
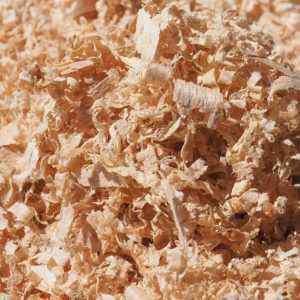
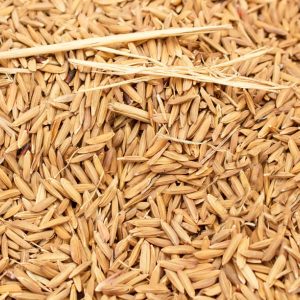
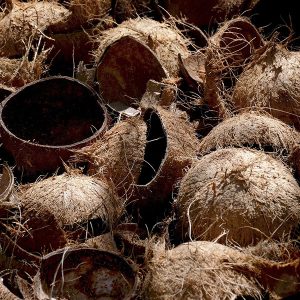
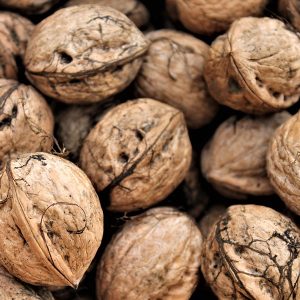
Mingjie biomass charcoal machine has a wide range of raw materials. It is suitable for making bamboo charcoal, wood charcoal, rice husk charcoal, straw charcoal, coconut shell charcoal, palm shell charcoal, sawdust charcoal, bagasse charcoal, etc.
Biomass, as a rich renewable resource, is widely found in agricultural waste (straw and rice husk), forestry waste (wood chips and bark), and urban organic waste. Biomass pyrolysis equipment converts biomass into high value-added product biochar through high temperature pyrolysis technology. At the same time, the biomass carbonization project can also realize the innovative project of resource recycling and carbon reduction.
Biomass charcoal making machine can not only realize the resource utilization of waste, but also play an important role in soil improvement and carbon sequestration.
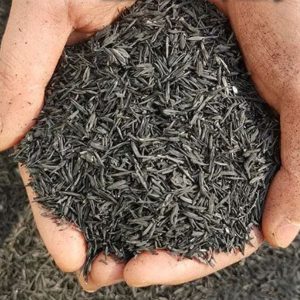
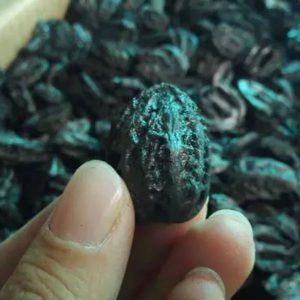
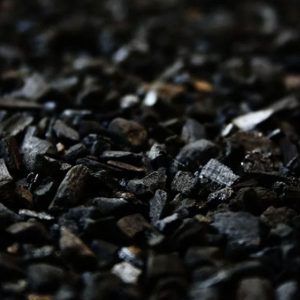
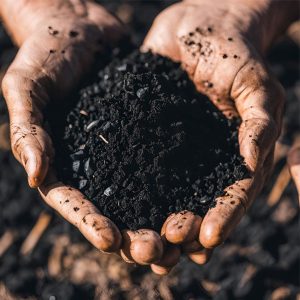
Biochar, as the product of biomass carbonization plant, has high added value. It can be used in soil conditioner, activated carbon and other fields.
Biochar has a rich pore structure and can effectively improve the soil structure. It can increase the air permeability and water permeability of the soil, making the soil more loose. At the same time, biochar can also improve the water retention capacity of the soil and reduce the evaporation and loss of water.
Biochar itself is rich in carbon and a variety of minerals and trace elements, such as potassium, calcium, magnesium, etc., which are essential nutrients for the growth of crops. After biochar is applied to the soil, it will gradually release these nutrients to provide long-term nutritional support for crops.
Moreover, biochar can also adjust the pH of the soil, making it more suitable for the growth of crops. For acidic soils, biochar can increase the pH value of the soil and reduce the harm of acidity to crops. For alkaline soils, biochar can play a certain buffering role and improve the chemical environment of the soil.
In addition, biochar can also absorb heavy metals and organic pollutants in the soil, reduce their toxic effects on crops, and ensure the quality and safety of agricultural products.
As a professional pyrolysis plant manufacturer, Mingjie Group offers pyrolysis solutions for different types of biomass. Please tell us the project you want to handle, and we will recommend you the suitable biomass carbonization equipment.
How does the Biomass Pyrolysis Plant work?
Preheat and Drying
Turn on the fuel burner to preheat the reactor for two hours. The fuel can be diesel, natural gas, liquefied petroleum gas or biomass pellets. When the reactor temperature reaches 150 degrees, you can start feeding. The chopped material is fed into the dryer through a high-angle conveyor.
The dryer is equipped with a high-speed rotating bladed dispersion shaft. It evenly distributes the material over the entire cylinder, increases the contact area of the material, and improves the drying efficiency.
Pyrolysis Carbonization
After drying, the material is fed into inner cylinder of carbonization reactor by conveyor and auto feeder. The material is deeply dehydrated and preheated in the inner cylinder of reactor, then move to outside cylinder of reactor through deflector.
The material remains in the carbonization reactors for about 15 to 25 minutes, so as to complete the biomass pyrolysis carbonization process.
Product Collection and Disposal
The biochar is continuously discharged from the reactor outer cylinder. It is transported to packaging bags or storage tanks by a water-cooled discharge screw. The water jacket of the discharge screw reduces the temperature of the biochar and ensures safe storage.
During the carbonization of waste biomass, the material releases mixed gases. These gases are first dedusted by a cyclone dust collector, and then separated into tar and wood vinegar by a condenser.
It contains a small amount of non-condensable combustible gas. Most of the combustible gas is recycled to the combustion chamber for heating the reactor, at which time the initial heating fuel can be stopped. Excess carbonized materials are burned directly outside the combustion chamber to reduce the pressure of the reactor.
During the entire biochar production process, the cooling pool provides cooling water for multiple systems. Including the biochar discharge screw, the condenser in the spray tower, and the cooling tower. The water is recycled throughout the process.
Flue Gas Purification
The high-temperature flue gas generated during the biomass pyrolysis process is cooled by the flue condenser and then enters the dust collector for further purification. The flue gas in the heating chamber can be used as a heat source for the dryer, so the dryer does not need additional fuel.
After drying, the flue gas mixed with water vapor is first dedusted by a cyclone dust collector. Then, it enters the spray tower and is purified by water washing, ceramic ring adsorption and water spraying. The flue gas will be further filtered by ultraviolet rays, oxygen and activated carbon adsorption, and finally discharged into the atmosphere.
Pyrolysis Process of Biomass Carbonization Plant
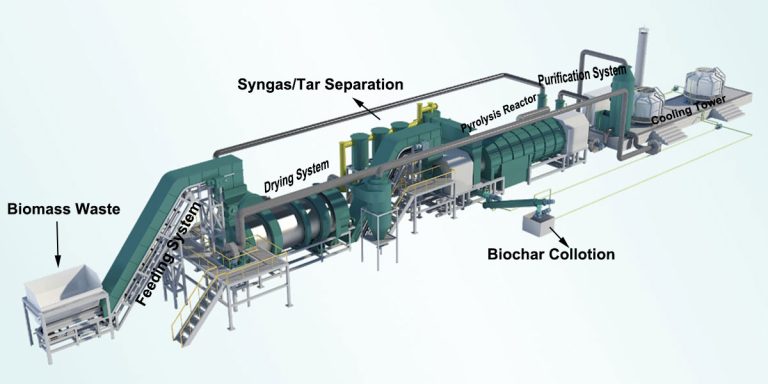
Waste biomass pyrolysis technology is a method of heating agricultural waste at high temperature under anaerobic conditions, converting biomass into biochar. Generally, the waste biomass raw materials need to be crushed and dried. Ensure that the feed size is crushed to less than 20mm and the moisture content is reduced to less than 15% to improve the pyrolysis efficiency.
During the waste biomass pyrolysis plant working process, there will be different reaction stages inside the pyrolysis reactor depending on the temperature range. For example, in the range of 250℃ – 750℃, the carbohydrate structure of biomass waste disintegrates to produce biomass charcoal, wood vinegar and combustible gas.
In an oxygen-free or oxygen-limited environment, biomass waste undergoes a series of pyrolysis reactions to achieve biochar and syngas conversion. Snygas is used for its own use, the flue gas generated during the biochar production equipment working process is also reused. Therefore, the biomass carbonization process is environmentally friendly and smokeless, which not only improves the working environment, but also promotes the efficiency of the carbonization furnace.
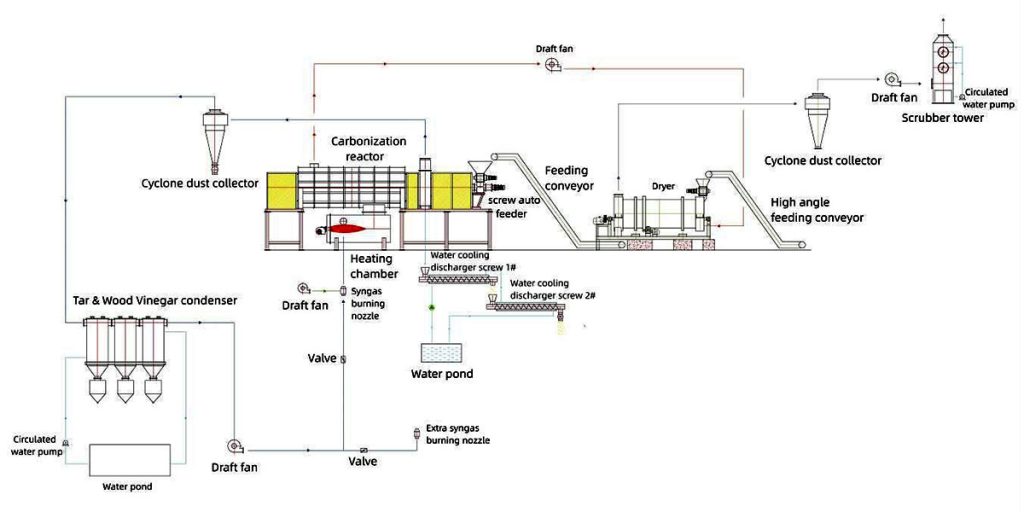
3 Stages of Pyrolysis Process
Drying stage: The temperature is below 150℃, and the water content of the biomass raw materials evaporates by external heat supply.
Endothermic pyrolysis stage: 150-300℃, the raw materials begin to decompose and release gaseous products (such as CO, CO₂, H₂S). The chemical composition of the raw materials begins to change, and different materials begin to pyrolyze at different temperatures.
Carbonization stage: The temperature is 300-600℃, and polycondensation and thermal decomposition reactions are the main reactions. A large amount of volatile matter is precipitated from the biomass raw materials, and the products precipitated during the carbonization process (such as tar, methanol, and ethylene) are all produced in this stage.
Key Points in Biomass Pyrolysis Process
The key conditions in the biomass pyrolysis carbonization process are pyrolysis temperature, holding time and heating rate.
Pyrolysis Temperature
Biochar preparation is usually carried out at 300-800 ℃, and the characteristics of biochar prepared at different temperatures will vary greatly.
The biochar yield obtained at low temperature (300-400 ℃) is high, but the pore structure is generally not obvious.
Biochar at high temperature (400-800 ℃) has a rich pore structure and a large specific surface area. It has better adsorption performance, but the yield may be reduced.
Insulation Time
After the pyrolysis temperature reaches the target temperature, it needs to be maintained for a period of time. This ensures that the raw materials are fully decomposed and formed stable biochar structure. The length of the holding time will affect the degree of carbonization and the properties of the biochar.
Heating Rate
The carbonization heating rate has a great influence on the yield of carbonization products. A high heating rate can make the material precipitate more tar and coal gas, reducing the yield of carbonized materials.
Slow heating (such as 5-10 ℃/min) helps to control the pyrolysis process and reduce the generation of tar and gas caused by too fast cracking. It can improve the yield and stability of biochar.
When the heating rate is reduced, the material is heated for a long time in the low temperature zone, and the selectivity of the pyrolysis reaction is stronger. The initial pyrolysis breaks the weaker bonds in the material molecules, and parallel and sequential thermal polycondensation reactions occur, forming a structure with high thermal stability. This reduces the yield of volatiles in the high-temperature stage of thermal decomposition, and obtains a higher yield of solid carbonization products (carbonized materials).