In January 2018, we received feedback from our Colombian customers. Their waste tire pyrolysis plant project has started operation, and they deal with a large amount of waste tires every day. Pyrolysis plant can convert waste tires into fuel oil, carbon black, steel wire and synthesis gas.
Their waste tire pyrolysis products have a broad market space. For example, pyrolysis oil is used as an alternative fuel, and carbon black has good applications in rubber, plastic and other industries. The recycled steel wire is directly sold to steel companies to achieve secondary utilization of resources and obtain profits.
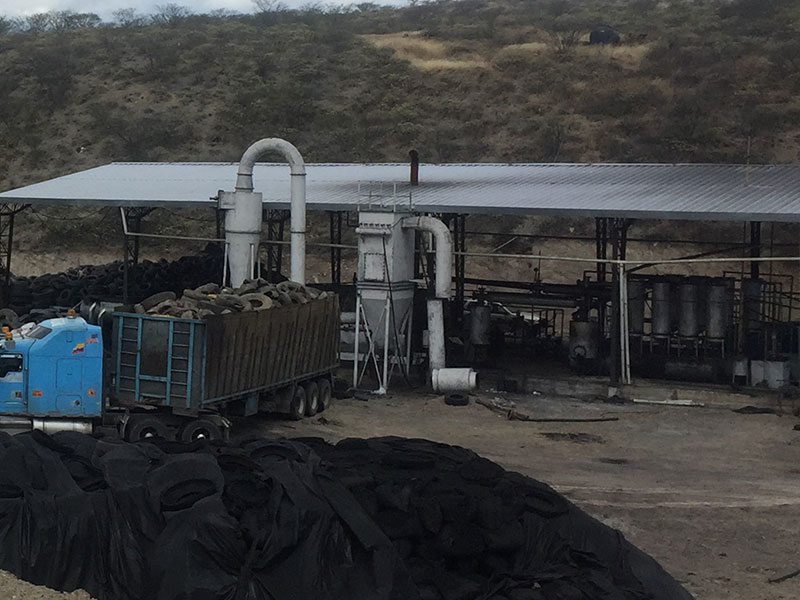
Waste Tyre Pyrolysis Project in Colombia
The Colombian government attaches great importance to environmental protection and resource recycling. It has actively formulated and issued a series of policies and regulations that are conducive to the development of waste tire pyrolysis projects.
In terms of taxation, enterprises engaged in waste tire pyrolysis treatment are given tax exemptions for a certain period of time. This reduces the operating costs of enterprises and improves their profitability.
In terms of subsidy policies, special subsidy funds are provided to enterprises that newly build waste tire pyrolysis projects. Support enterprises to purchase advanced equipment, conduct technological research and development and innovation, and help enterprises expand their production scale.
At the same time, the government has also optimized the project approval process and simplified the procedures. This improves the approval efficiency and creates a good policy environment for the rapid implementation of the project.
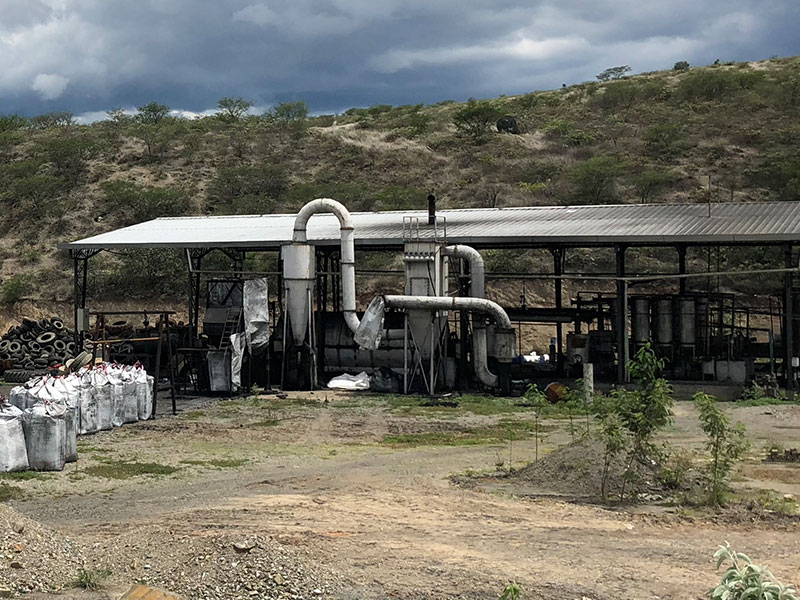
Advantage of Waste Tyre Pyrolysis Project
The waste tyre pyrolysis project in Colombia has significant economic benefits and environmental advantages.
The products such as pyrolysis oil, pyrolysis carbon black and steel wire produced after the pyrolysis of waste tires have high economic value.
The waste tyre pyrolysis project realizes the harmless, reduced and resource-based treatment of waste tires. The pyrolysis gas generated during the pyrolysis process is purified and discharged in compliance with the emission standards, reducing the emission of harmful gases. Products such as pyrolysis oil and pyrolysis carbon black are effectively recycled, realizing the recycling of resources.
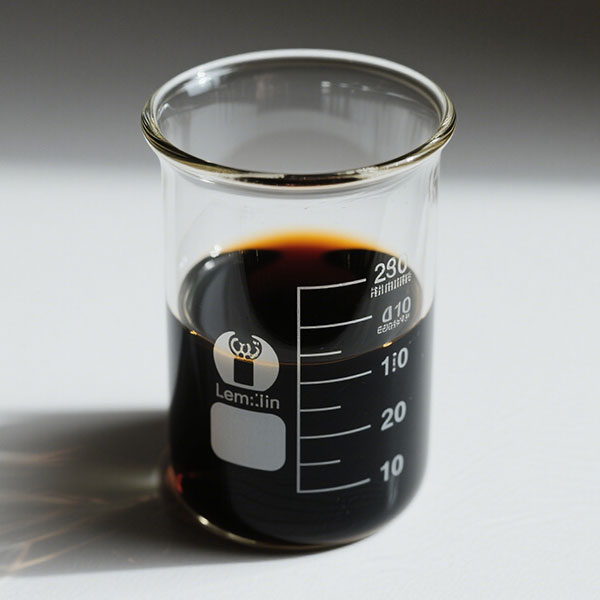
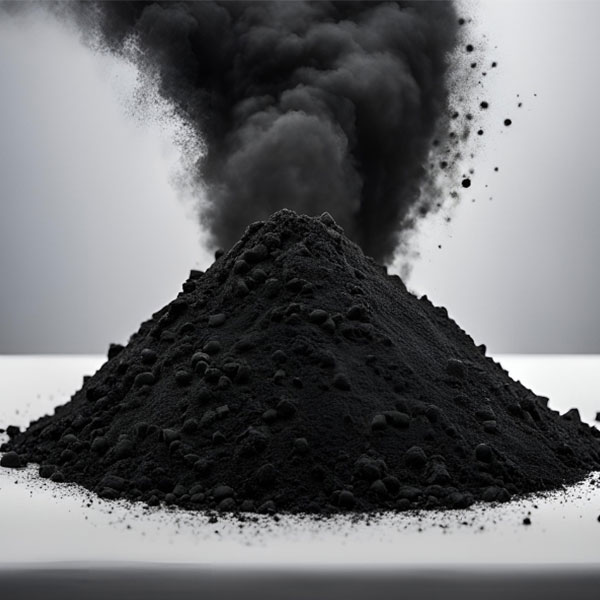
Treatment Process of Waste Tire Pyrolysis Plant
Pretreatment Stage
Preliminary screening of waste tires to remove large impurities. Use professional equipment to remove steel wires from tires. The entire tire can be directly heated and processed by batch pyrolysis plant. Continuous pyrolysis plants require tires to be crushed and the feed size should be less than 5-8mm.
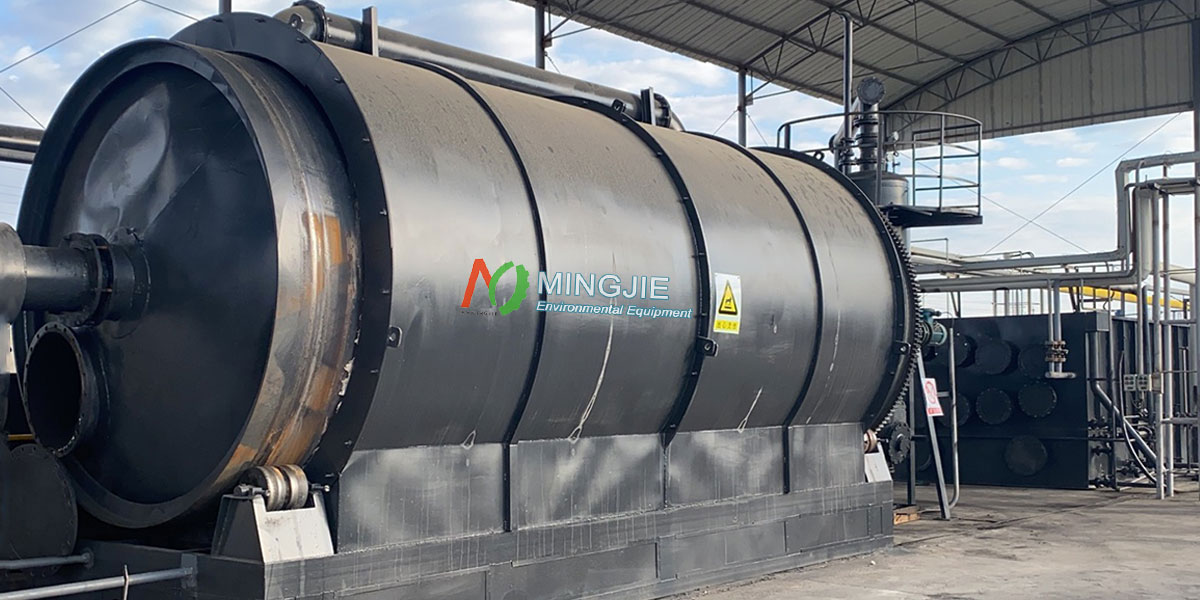
Pyrolysis stage
The waste tire is fed into the pyrolysis reactor. Under the condition of oxygen isolation, the temperature in the reactor is gradually raised to the set temperature by external heating.
As the temperature rises, the tire begins to undergo pyrolysis. It gradually transforms into products such as pyrolysis gas, pyrolysis oil and carbon black.
The synthesis gas produced during the pyrolysis process has a high calorific value. It can be returned as fuel to maintain the heat required for the pyrolysis reaction.
Product Separation and Refining Stage
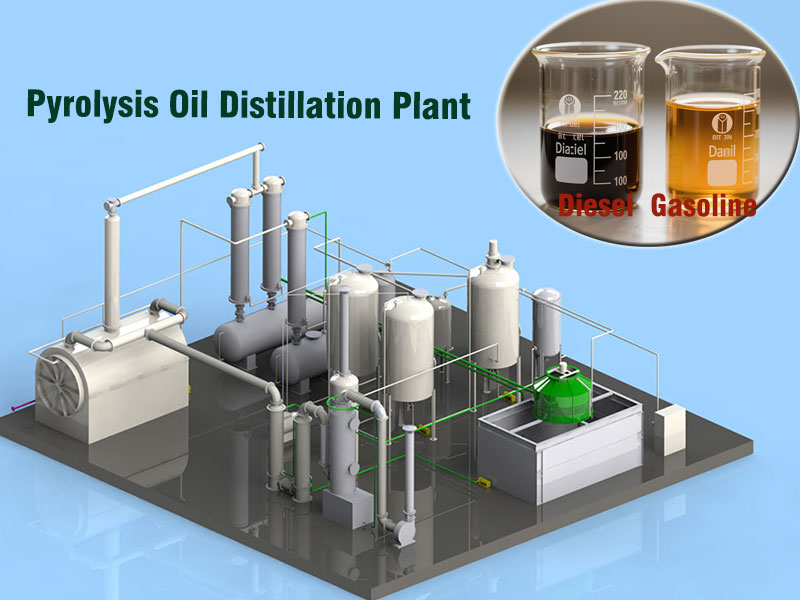
The mixed product discharged from the pyrolysis reactor first enters the condenser, where the pyrolysis oil is condensed into liquid. After being separated from water by the oil-water separator, the crude pyrolysis oil is collected.
Crude pyrolysis oil usually contains impurities and some undesirable components. It needs to be further purified by distillation equipment.
Carbon black is discharged from the bottom of the condenser. It is screened, ground and processed to remove the residual impurities and improve the purity and quality of carbon black. It can be used in rubber products, inks, coatings and other industries.