In 2017, Mingjie Group completed the installation of plastic pyrolysis equipment for sale to Romania. This is a set of continuous pyrolysis equipment, it can process 12 tons of plastic per day. The continuous pyrolysis plastic equipment is equipped with automatic feeding system and and slag discharge system. It can achieve 24-hour fully continuous feeding and discharging.
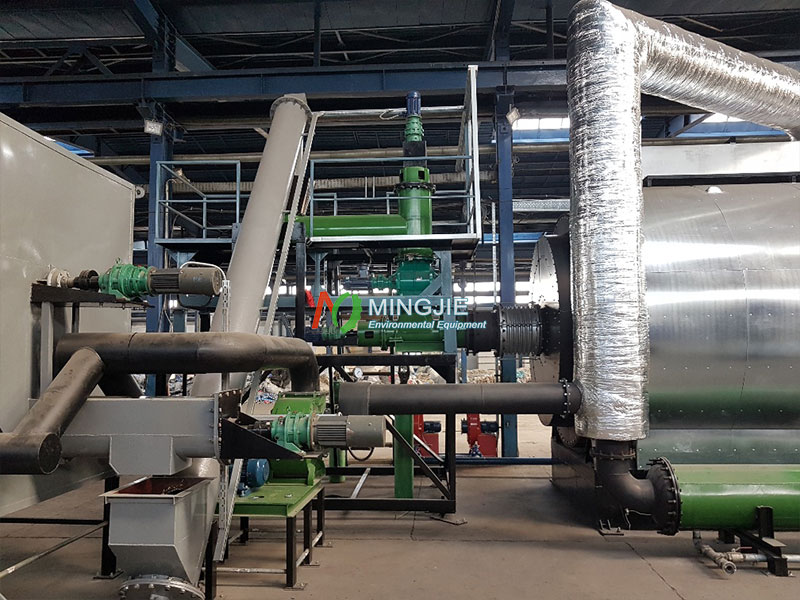

The continuous plastic pyrolysis equipment can continuously process waste plastics. From feeding to discharging, the entire pyrolysis plant is sealed and the operating environment is clean. The continuous plastic waste pyrolysis process has the advantages of reliability and safety, high efficiency, low operating cost, and automatic control.
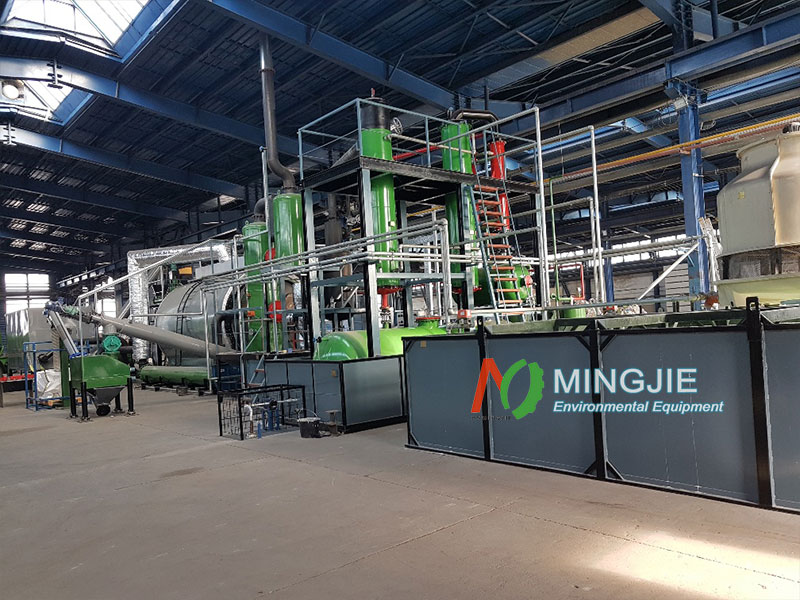
Continuous Plastic Pyrolysis Equipment for Sale
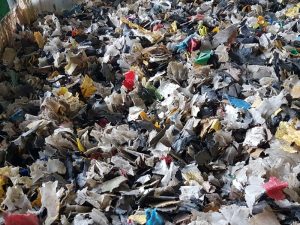
Mingjie continuous pyrolysis plant is divided into semi-automatic continuous pyrolysis plant and fully continuous pyrolysis plant. Continuous plastic pyrolysis equipment has strict requirements on feed size, and the crushed plastic must be less than 5-8mm.
The continuous waste plastic pyrolysis equipment is mainly composed of a feeding system, a pyrolysis device, an oil and gas cooling system, a non-condensable gas purification system, a discharging system, a flue gas purification system, a circulating cooling water system, and a PLC intelligent control system.
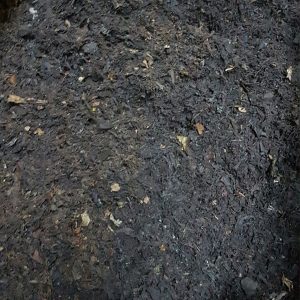
Plastic Waste Pyrolysis Process
The continuous plastic pyrolysis equipment realizes fully enclosed, continuous, and environmentally friendly production. The pyrolysis plant can convert waste plastics to obtain pyrolysis oil and carbon black new energy.
Pretreatment of Waste Plastics
Send the waste plastics into the crusher for crushing so that its size meets the feeding requirements of less than 5-8mm. The finely crushed waste plastics are discharged to the waste plastic air-drying area through a belt conveyor, and the moisture is reduced to 20% by using the residual heat of the pyrolysis flue gas. This can reduce the energy consumption of the pyrolysis system and the amount of pyrolysis wastewater generated.
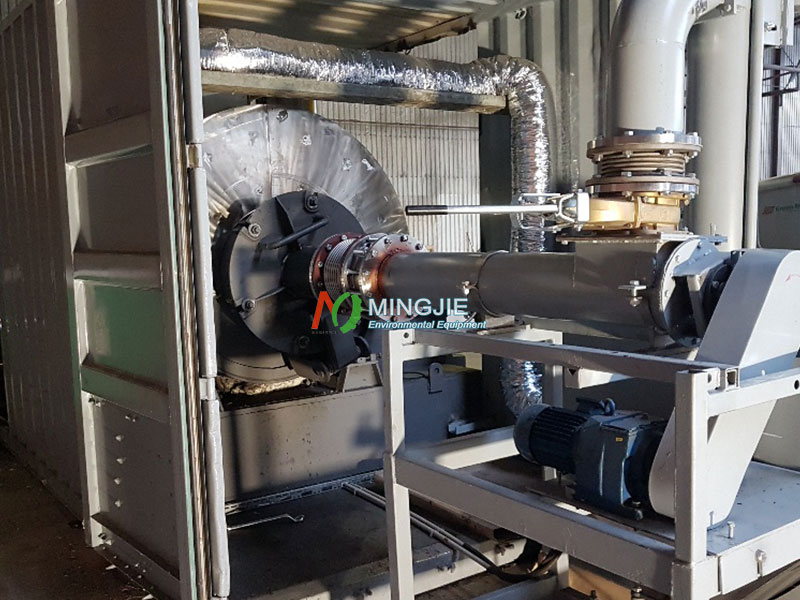
Feeding
The feeding system consists of a loading bin, a conveyor belt and a screw propeller. The air-dried waste plastic is sent to the pyrolysis reactor via a belt conveyor.
- When the conveyor belt starts feeding, the transition chamber needs to close the valve below and open the valve above. When the transition chamber is full of materials, the valve above the transition chamber needs to be closed to pause.
- Open the exhaust valve above the transition chamber. The exhaust valve is connected to the vacuum pump, and the oxygen in the transition chamber is extracted under the action of the vacuum pump. When the negative pressure gauge shows a negative number in the transition chamber, the transition chamber is in an oxygen-free or negative oxygen state, and the exhaust valve is closed at this time.
- Open the discharge valve below the transition chamber and send the oxygen-free material into the screw propeller. At this time, turn the screw propeller to push the material into the main cracking furnace. Then the main furnace is ignited and rotated to start pyrolysis.
During the plastic waste pyrolysis process, continuous feeding can be carried out, and the synthesis gas in the main furnace is led out of the furnace by a micro-negative pressure process. Carbon black is sent to the carbon black slag discharge system along with the screw propeller.
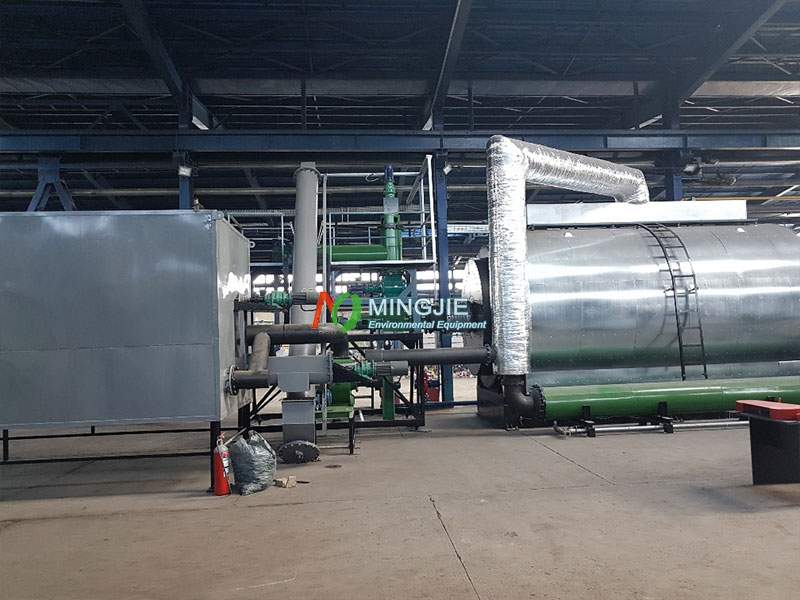
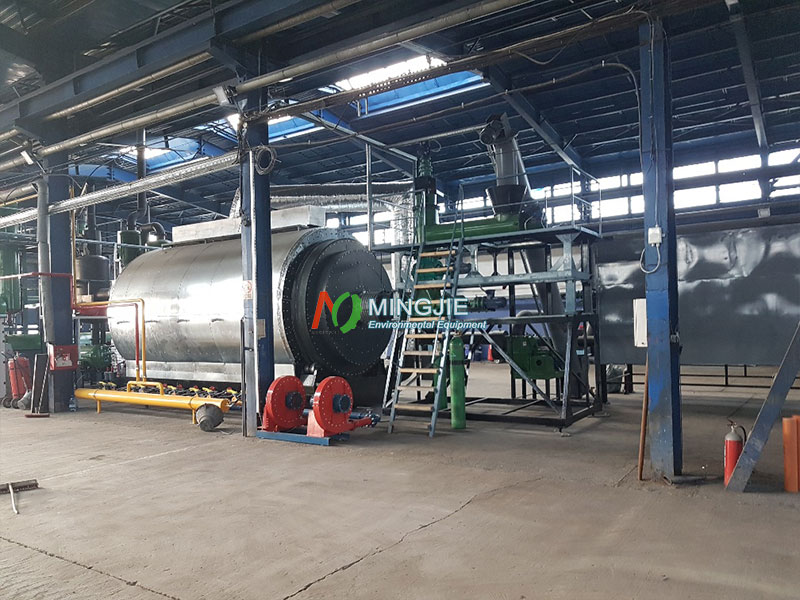
Continuous Plastic Waste Pyrolysis Process
The pyrolysis chamber uses pyrolysis synthesis gas for combustion heating. Diesel or natural gas is used to heat the pyrolysis reactor when starting the furnace. The plastic pyrolysis plant is equipped with a digital temperature controller. The temperature of the pyrolysis furnace is automatically controlled at 400-450℃ according to the set temperature control requirements.
The plastic waste pyrolysis process is carried out layer by layer from the outside to the inside. The pyrolysis products are gas and solid phases. The gas phase is discharged from the furnace cavity under the pressure difference caused by the temperature difference inside and outside the pyrolysis furnace, and is sent to the condensation system as pyrolysis gas for condensation. The remaining residual carbon is cooled and packaged as a product.
Cooling Process
The condensation system uses water cooling. The cooling water is supplied by a circulating water pool.
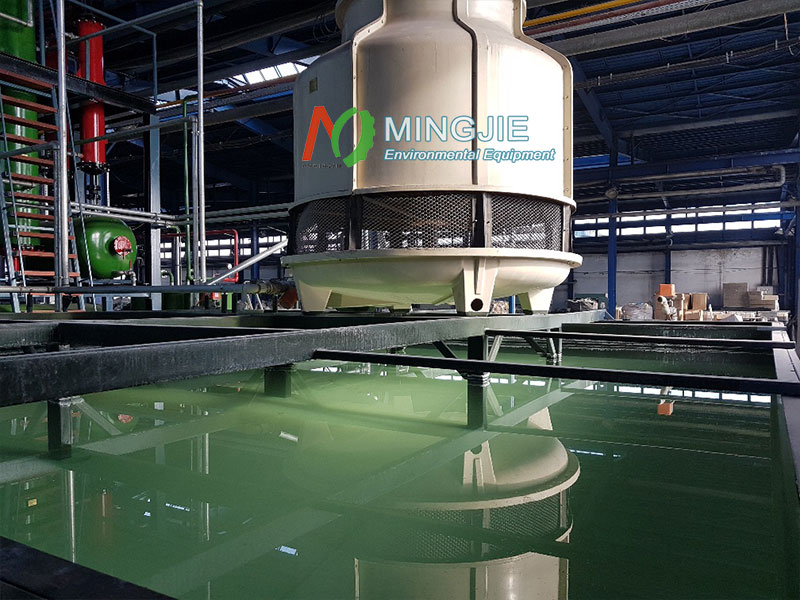
The pyrolysis oil and gas enter the gas separation bag and are subjected to gravity sedimentation to remove fine dust. Then they enter the condenser and extract most of the residual gas in the system. The condensable part becomes liquid and enters the oil storage tank through the separation tank, and the non-condensable part enters the purification device.
Oil and water are separated in the separation tank, and a small amount of oily wastewater is produced. The pyrolysis fuel oil enters the oil storage tank for storage.
The non-condensable gas is vacuumed into a buffer tank by a vacuum pump. Under the action of vacuum negative pressure, the non-condensable gas enters the purification device through the condensation device, and after water sealing, it passes through the flame retardant and then goes to the furnace combustion chamber for combustion. The vacuum pump can reduce the pressure in the pyrolysis reactor to a slightly negative pressure state.
The condensed exhaust gas passes through two safety devices, the water seal and the backfire arrester. Then, it is sent to the combustion chamber of the pyrolysis furnace as fuel to provide energy. The combustion flue gas is treated by the purification system and discharged through the chimney after meeting the standards.
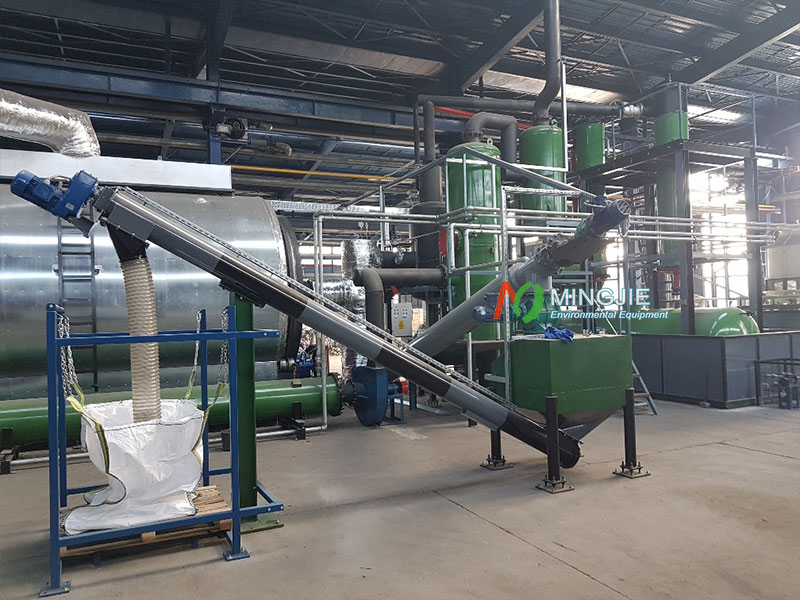
Carbon Black Slag Discharge
The carbon black produced after pyrolysis is transported to the packaging bag by the spiral slag cooler. The carbon black slag discharge is fully enclosed. Circulating cooling water is introduced into the outer wall of the slag cooler, and the temperature of the carbon black is reduced to below 40℃ during the spiral conveying process.